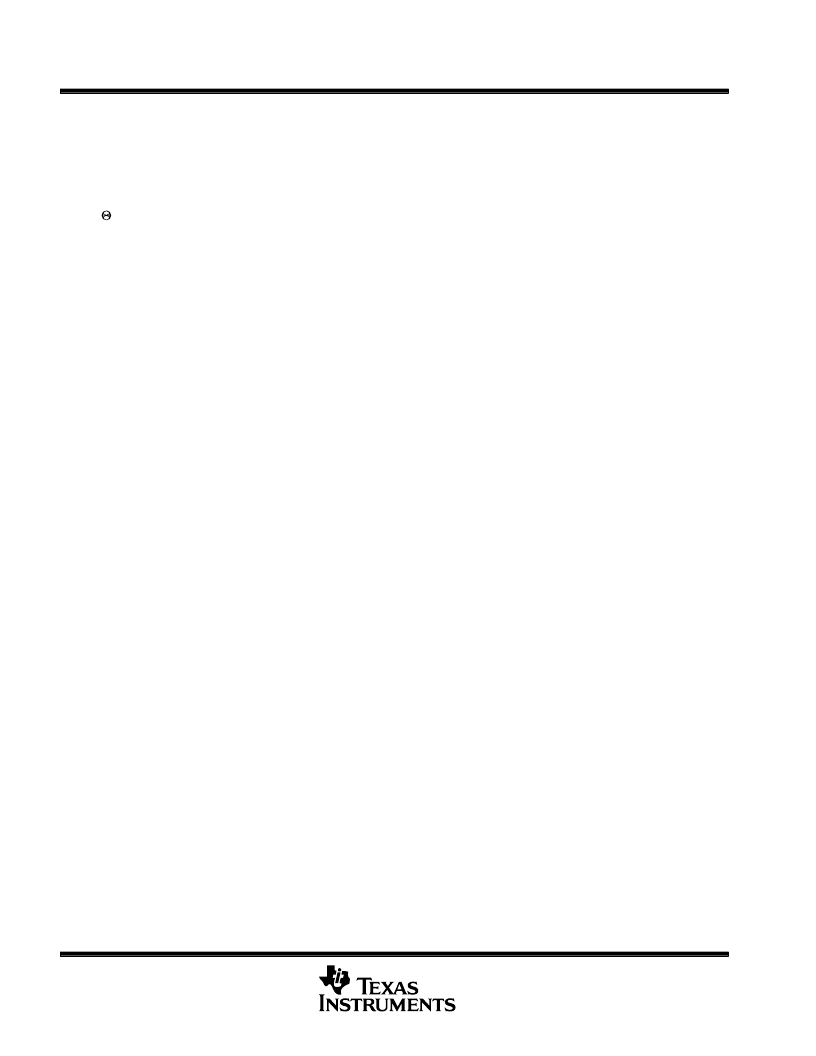
TMX320C6201
DIGITAL SIGNAL PROCESSOR
SPRS051B – JANUARY 1997 – REVISED JUNE 1997
36
POST OFFICE BOX 1443
HOUSTON, TEXAS 77251–1443
heat-sink selection procedure
Most of the current consumed by CMOS devices is alternating current (AC), which is charging and discharging
the capacitances of internal nodes, pins, and the external pin loads. The current flowing through the ’320C6201
causes the temperature of the silicon die to rise. To maintain device reliability and proper operation, the junction
temperature must not exceed the maximum specified junction temperature. As the heat is transferred from the
die to the package, the case temperature of the package also rises. The junction-to-case thermal resistance
R jc, together with the maximum junction temperature, are parameters that determine maximum case
temperature T
CMAX
. Because of these factors, the specification of temperature is given in terms of T
CMAX
in
the recommended operating conditionssection of this document.
From the case, the heat typically flows to the surrounding air up through the heat sink and down through the
pins and the board (see Figure 19). The heat dissipation through the board material largely depends on the
number of power and ground layers inside the board. The portion of the power that is dissipated by the heat
sink must first propagate through the case-sink joint. The thermal resistance of case to sink joint can vary,
depending on the type of joint used. The rate at which the heat is transferred from the sink to ambient air depends
on the velocity of the air at the heat sink. The heat flow from the sink rises with the speed of the airflow. The
objective of the examples in this section is to present a method for first-order approximation of the size of the
heat sink needed to keep the maximum case temperature from exceeding the T
CMAX
during maximum system
operating conditions. Following heat sink installation, the actual case temperature must be measured to verify
that if does not exceed the T
CMAX
value.
Heat-transfer analysis can be a complex task depending on the degree of accuracy required in modeling of
system components. A number of computational fluid dynamics and heat-transfer tools is available to provide
highly accurate results; however, data must be verified using test methods. This document uses a simplified
approach to select a heat sink that matches a particular operating environment. The driving parameter in
determining the heat flow is the maximum case temperature which must stay below T
CMAX
at all times during
device operation. The system parameters that have first-order effect on the case temperature are the average
device power dissipation, ambient air temperature, and air approach velocity. The choice of the heat sink largely
depends on those factors as shown in the following examples. Other factors that may affect the heat dissipation
include board design/materials and the case-to-sink attachment method. The relatively long time constant of
the case/sink combination (around two minutes) can effectively smooth out any power peaks that occur. To
validate proper operation of the heat sink, a small hole must be drilled in the center of the sink for placement
of a miniature thermocouple directly on the case (center top surface) for measuring the actual case temperature
under system maximum expected operating conditions (see Figure 19).
P