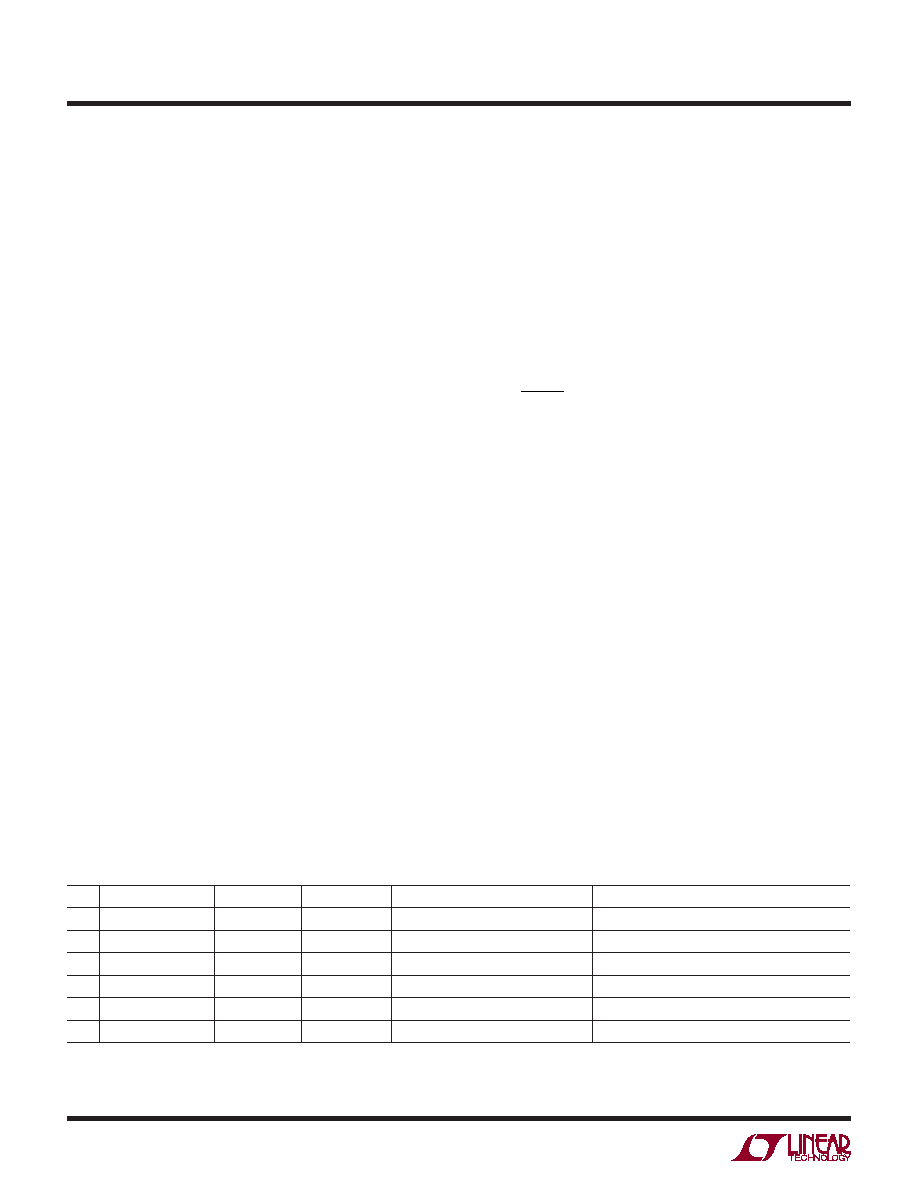
LTC4110
44
4110fb
Table 10. Recommended Components Values for 12V Input Supply Li-Ion Battery Backup System Manager
Cell
MAX (ICHG, ICAL) (A) RSNS(BAT)(mΩ)RSNS(FET)(mΩ)
TRANSFORMER INDUCTANCE (μH)
TRANSFORMER VENDOR AND PART NUMBER
3
1
100
50
24
BH 510-1019 TDK PCA14.5/6ER-U03S002
3
2
50
25
12
COILTRONICS VP4-0140-R
3
33
15
9
TDK PCA20EFD-U04S002
4
1
100
50
24
COILTRONICS VPH4-0140-R
4
2
50
25
12
COILTRONICS VPH4-0075-R
4
3
33
15
9
COILTRONICS VP5-0155-R
Note: 1:1 turns ratio for all the transformers listed in the table..
that the power dissipated is never allowed to rise above
the manufacturer’s recommended maximum level.
Switching transition time is another consideration. When
the LTC4110 senses a need to switch any PowerPath
MOSFETs on or off time delays are encountered. MOSFETs
with higher QGATE will require more bulk capacitance on
DCOUT to hold up all the system’s power supply function
during the transition. The transition time of a MOSFET to
an on or off state is directly proportional to the MOSFET
gate charge. Switching times are given in the Electrical
Characteristics Table (see tdDON, tdDOFF).
TRANSFORMER
There are two ways to design a transformer.
1. Design it yourself.
2. Work with a transformer vendor to identify an off-
the-shelf transformer.
Even if you choose to design it yourself, you still have to
nd a transformer manufacturer to make it for you.
We recommend contacting a transformer manufacturer
directly since they often have online tools that can help
you quickly nd and select the right transformer. There are
many off the shelf transformers that can be successfully be
used with the LTC4110. Table 10 shows some suggested
off the shelf transformers.
If you want to design a custom transformer optimized
for your design, Application Note 19 has an example of
how to design a Flyback transformer in the “Transformer”
section.
APPLICATIONS INFORMATION
Regardless of which way you go, we offer the following
thoughts.
Turns ratio affects the duty factor of the power converter
which impacts current and voltage stress on the power
MOSFETs, input and output capacitor RMS currents and
transformer utilization (size vs power). Using a 50%
duty factor under nominal operating conditions usually
gives reasonable results. For a 50% duty factor, the turns
ratio is:
N
V
BAT
DCIN
=
VBAT is the nominal battery voltage. N should be calculated
for the design operating in charging mode and in calibration
mode. The nal turns ratio should be chosen so that it is
approximately equal to the average of the two calculated
values for N. In addition, choose a turns ratio which can
be made from the ratio of small integers. This allows
bilar windings to be used in the transformer, which can
reduce the leakage inductance and the need for aggressive
snubber design, thus improving efciency.
Avoid transformer saturation under all operating conditions
and combinations (usually the biggest problems occur at
high output currents and extreme duty cycles). Choose
the magnetizing inductance so that the current ripple is
about 20% of DC current.
Finally, in low voltage applications, select a transformer
with low winding resistance. This will improve efciency
at heavier loads.