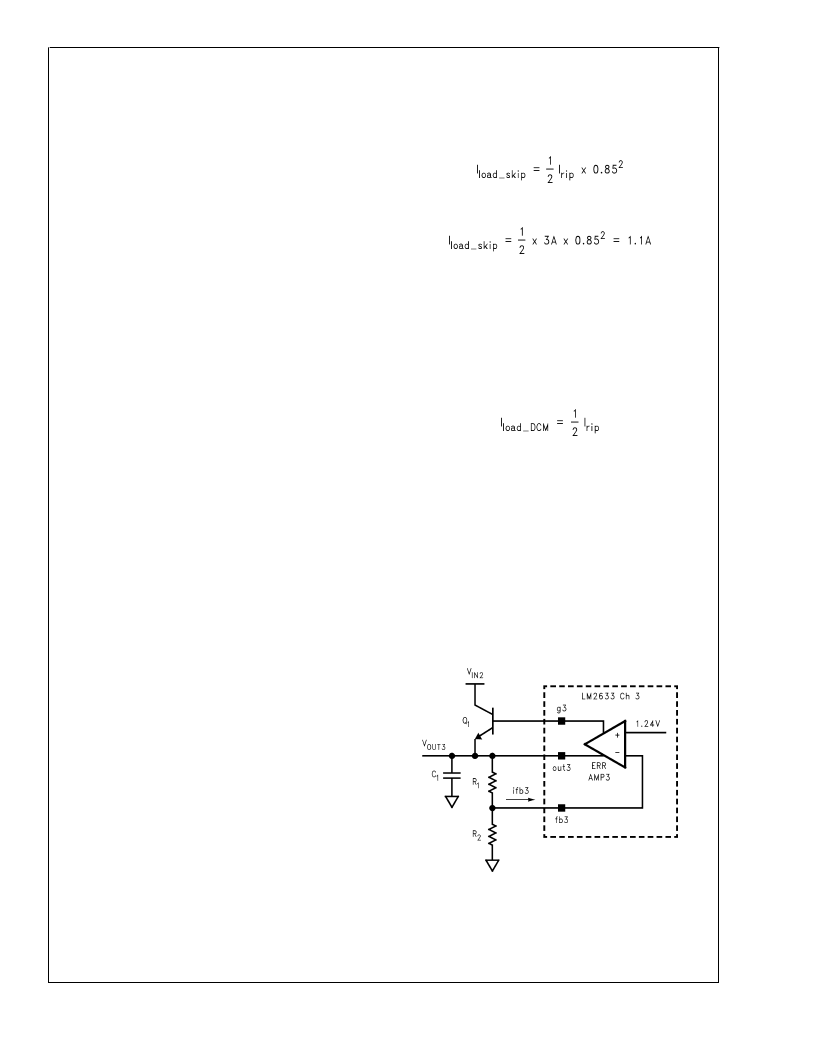
Control Loop Design
(Continued)
If aluminum, tantalum or OSCON capacitors are going to be
used, make sure the combined ESR is not greater than
10.6 m
.
Depending on the application, a different priority may be
assigned to the selection of components. For example, to
achieve a 10.6 m
combined ESR, it would require 6
low-ESR tantalum capacitors, which can be quite expensive.
If the inductor size is allowed to expand, then a higher
inductance value can be used so that ripple current is re-
duced and impedance of the capacitor at the switching fre-
quency can be higher. It is often necessary to go through
several iterations before a reasonable combination of the
inductor and capacitors is achieved.
Notice the above procedure is given without any consider-
ation of a load transient, whether expected or unexpected.
The power supply designer may be tempted to use a 100 μF
ceramic capacitor as the only output capacitor in the above
example. That may be fine in a design that has a very static
load. However, should there be a large fault load current
(which is not enough to trigger UVP) and if later that condi-
tion is suddenly lifted, the output may see a severe over
voltage. Although the LM2633 will shut down immediately
upon seeing the over-voltage event, the load could have
been damaged already. Another concern with pure ceramic
output capacitors is soft start. It may be necessary to in-
crease the soft start time so that there will be minimum
overshoot at the end of soft start. So when a large induc-
tance and a small capacitance are chosen, care should be
given to the above situations.
If the load current goes from one level to another during
normal operations, a design with less capacitance tends to
have more output voltage excursion and recover more
slowly
than
one
with
more
time-domain viewpoint, that is because less capacitance is
less effective an energy buffer when the load current is
temporarily different from the inductor current. From the
frequency-domain viewpoint, that is because the output im-
pedance of the regulator is higher.
For power supplies that don’t have a stringent load transient
requirement, polymer aluminum capacitors can be used as
well as low-ESR tantalum capacitors. These polymer alumi-
num capacitors are surface mount, long-life, ignition free and
typically have very low ESR values. For example, Cornell
Dubilier’s ESRE and ESRD polymer aluminum chip capaci-
tors have ESR value as low as 6 m
and capacitance up to
270 μF (http://www.cornell-dubilier.com).
Panasonic also offers specialty polymer aluminum capaci-
tors. Panasonic’s UE series offers capacitance up to 270 μF,
and voltage rating up to 8 VDC.
For the Typical Applicationcircuit, if there is no stringent load
transient requirement on Channel 1, C2 can be replaced by
a
single
polymer
aluminum
ESRE271M02R from Cornell Dubilier. The frequency com-
pensation should be: C14 = 4.7 nF, R9 = 7.5 k
. C15 and
R10 are not necessary. Notice that the voltage rating of that
capacitor is only 2 VDC.
capacitance.
From
the
capacitor,
such
as
Designing Around the Pulse-Skip Mode
If the FPWM pin is pulled to logic high, the LM2633 operates
in pulse-skip mode. In this mode, when the load is light
enough, the LM2633 starts to skip pulses. See Pulse-Skip
Mode in Operation Descriptions
In pulse-skip mode, the apparent switching frequency is
lower than the frequency the regulator would run at if it were
in force-PWM mode. The actual frequency depends on the
load, the lighter the load the lower the frequency.
The load at which pulse-skipping starts to happen can be
determined from the following formula:
(59)
Example: I
rip
= 3A.
Since the critical load current completely depends on the
inductor ripple current, the inductance value cannot be arbi-
trary if accurate control of the value of the critical load is
desired.
When the FPWM pin is pulled high, the regulator enters the
discontinuous conduction mode (DCM) when the load is light
enough so that the inductor current goes to zero before the
end of each switching cycle. The critical load current value
for the regulator to enter DCM is:
(60)
Notice in DCM mode the FETs still switch every clock cycle
but the duty cycle shrinks as load current decreases. When
the load current goes below I
, the regulator enters
the pulse-skip mode. So the DCM region is a very narrow
one.
So, when the peak-peak ripple current is 3A, the DCM
happens only when load current falls in the 1.1A to 1.5A
range. Above that range, the regulator is in continuous con-
duction mode (CCM), and below that range, the regulator
runs in pulse-skip mode.
Designing a Linear Regulator with Channel 3
Channel 3 of the LM2633 can be used to drive an external
NPN transistor and provide linear regulation. See Figure 19
The output voltage is adjusted through the voltage divider,
and the equation is:
200008A7
FIGURE 19. Channel 3 Controlling an LDO
L
www.national.com
37