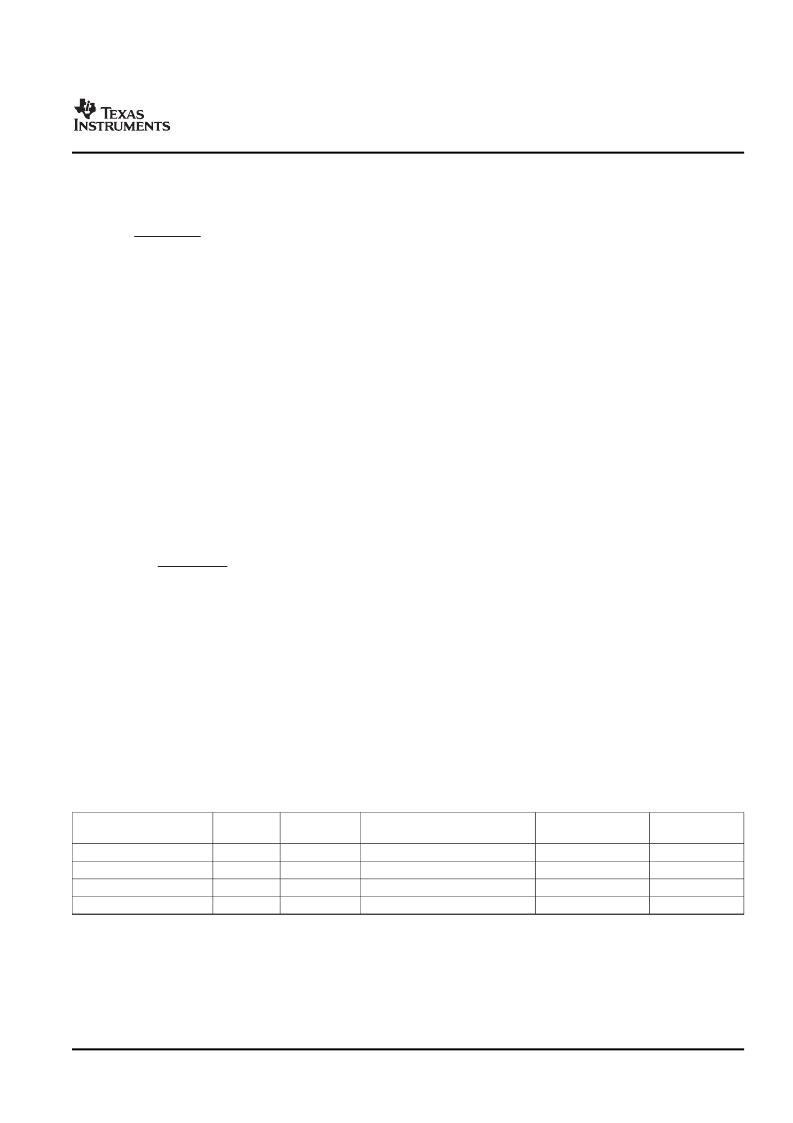
www.ti.com
SWITCH DUTY CYCLE
The maximum switch duty cycle (D) of the TPS61170 is 90% (min). The duty cycle of a boost converter under
continuous conduction mode (CCM) is given by:
D
Vout
Vin
Vout
(5)
INDUCTOR SELECTION
The selection of the inductor affects steady state operation as well as transient behavior and loop stability. These
factors make it the most important component in power regulator design. There are three important inductor
specifications, inductor value, DC resistance and saturation current. Considering inductor value alone is not
enough.
I
in_DC
Vout
Vin
Iout
(6)
TPS61170
SLVS789–NOVEMBER 2007
For a 5V to 12V application, the duty cycle is 58.3%, and for a 5V to 24V application, the duty cycle is 79.2%.
The duty cycle must be lower than the maximum specification of 90% in the application; otherwise, the output
voltage can not be regulated.
Once the PWM switch is turned on, the TPS61170 has minimum ON pulse width. This sets the limit of the
minimum duty cycle. For operating low duty cycle, the TPS61170 enters pulse-skipping mode. In this mode, the
device keeps the power switch off for several switching cycles to keep the output voltage in regulation. This
operation typically occurs in light load condition when the PWM operates in discontinuous mode. See the
Figure 12
.
The inductor’s value determines the inductor ripple current. It is recommended that the peak-to-peak ripple
current given by
Equation 3
be set to 30–40% of the DC current. Also, the inductor value should not be beyond
the range in the recommended operating conditions table. It is a good compromise of power losses and inductor
size. Inductor DC current can be calculated as
Inductor values can have ±20% tolerance with no current bias. When the inductor current approaches saturation
level, its inductance can decrease 20% to 35% from the 0A value depending on how the inductor vendor defines
saturation current. Using an inductor with a smaller inductance value forces discontinuous PWM where the
inductor current ramps down to zero before the end of each switching cycle. This reduces the boost converter’s
maximum output current, causes large input voltage ripple and reduces efficiency. In general, large inductance
value provides much more output and higher conversion efficiency. Small inductance value can give better the
load transient response. For these reasons, a 10
μ
H to 22
μ
H inductor value range is recommended.
Table 3
lists
the recommended inductor for the TPS61170.
TPS61170 has built-in slope compensation to avoid sub-harmonic oscillation associated with current mode
control. If the inductor value is lower than 10
μ
H, the slope compensation may not be adequate, and the loop can
be unstable. Therefore, customers need to verify the inductor in their application if it is different from the
recommended values.
Table 3. Recommended Inductors for TPS61170
L
DCR MAX
(m
)
90
237
144
247
SATURATION CURRENT
(A)
1.3
1.1
1.2
0.84
SIZE
PART NUMBER
VENDOR
(
μ
H)
10
10
10
10
(L
×
W
×
H mm)
5.2
×
5.2
×
3.0
5
×
5
×
2.0
5
×
5
×
2.4
4.5
×
3.2
×
2.0
A915_Y-100M
VLCF5020T-100M1R1-1
CDRH4D22/HP
LQH43PN100MR0
TOKO
TDK
Sumida
Murata
Copyright 2007, Texas Instruments Incorporated
Submit Documentation Feedback
15
Product Folder Link(s):
TPS61170