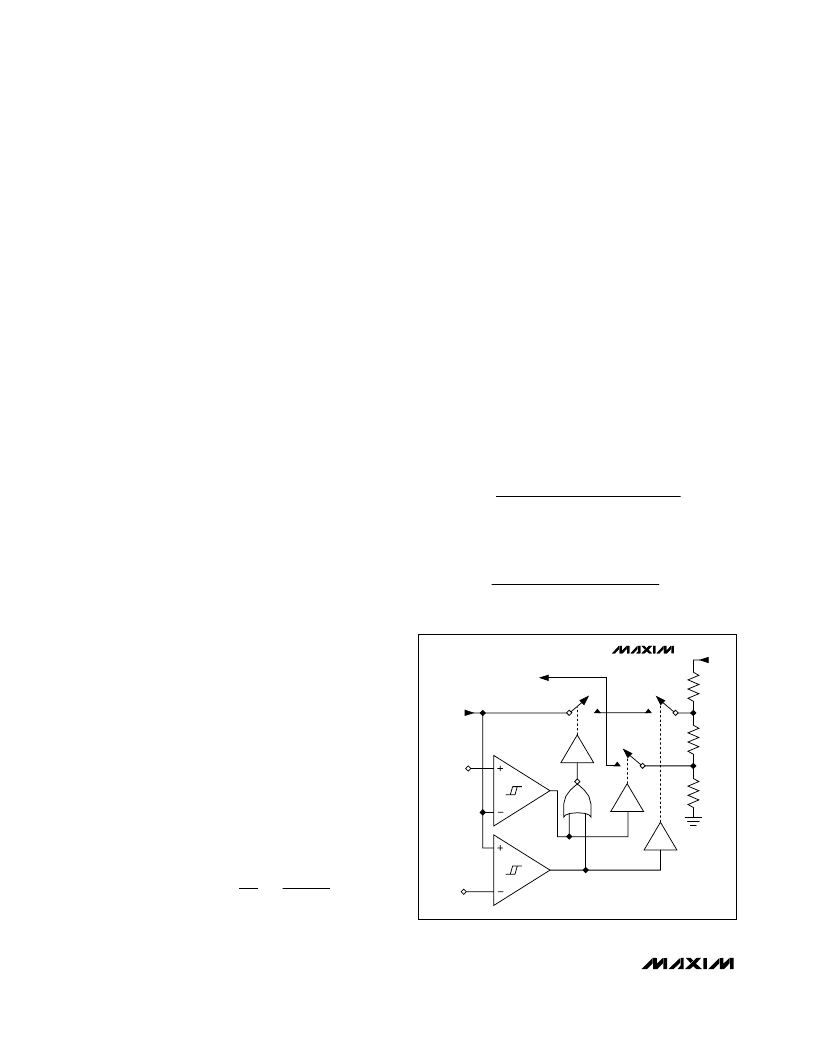
M
Maximum Load Current. There are two values to con-
sider. The peak load current (I
PEAK
) determines the
instantaneous component stresses and filtering
requirements and thus drives output capacitor selec-
tion, inductor saturation rating, and the design of the
current-limit circuit. The continuous load current
(I
LOAD
) determines the thermal stresses and thus
drives the selection of input capacitors, MOSFETs,
and other critical heat-contributing components.
Switching Frequency. This choice determines the
basic trade-off between size and efficiency. The opti-
mal frequency is largely a function of maximum input
voltage, due to MOSFET switching losses proportion-
al to frequency and V
IN
2
. The optimum frequency is
also a moving target due to rapid improvements in
MOSFET technology that are making higher frequen-
cies more practical.
Inductor Operating Point. This choice provides trade-
offs: size vs. efficiency and transient response vs. out-
put ripple. Low inductor values provide better
transient response and smaller physical size but also
result in lower efficiency and higher output ripple due
to increased ripple currents. The minimum practical
inductor value is one that causes the circuit to operate
at the edge of critical conduction (where the inductor
current just touches zero with every cycle at maximum
load). Inductor values lower than this grant no further
size-reduction benefit. The optimum operating point is
usually found between 20% and 50% ripple current.
When pulse skipping (
SKIP
= low at light loads), the
inductor value also determines the load-current value
at which PFM/PWM switchover occurs.
Setting the Output Voltage (Buck)
Preset Output Voltages
The MAX8632 dual-mode operation allows the selection
of common voltages without requiring external compo-
nents (Figure 5). Connect FB to GND for a fixed 2.5V
output, to AV
DD
for a fixed 1.8V output, or connect FB
directly to OUT for a fixed 0.7V output.
Setting the Buck Regulator Output (V
OUT
) with a
Resistive Voltage-Divider at FB
The buck-regulator output voltage can be adjusted from
0.7V to 5.5V using a resistive voltage-divider (Figure 6).
The MAX8632 regulates FB to a fixed reference voltage
(0.7V). The adjusted output voltage is:
where V
FB
is 0.7V, R
C
and R
D
are shown in Figure 6,
and V
RIPPLE
is:
Setting the VTT and VTTR Voltages (LDO)
The termination power-supply output (VTT) can be set by
two different methods. First, the VTT output can be con-
nected directly to the VTTS input to force VTT to regulate
to V
REFIN
/ 2. Secondly, VTT can be forced to regulate
higher than V
REFIN
/ 2 by connecting a resistive divider
from VTT to VTTS. The maximum value for VTT is V
VTTI
-
V
DROPOUT
where V
DROPOUT
= I
VTT
×
0.3
(max) at T
A
= +85°C.
The termination reference voltage (VTTR) tracks 0.5
V
REFIN
.
Inductor Selection (Buck)
The switching frequency and inductor operating point
determine the inductor value as follows:
(
×
×
For example: I
LOAD(MAX)
= 12A, V
IN
= 12V, V
OUT
=
2.5V, f
SW
= 600kHz, 30% ripple current or LIR = 0.3:
L
V
V
V
kHz
A
H
.
(
×
×
0 3
=
≈
2 5
12
12
600
12
1
- 2.5V)
μ
L
V
f
V
I
LOAD MAX
V
V
LIR
OUT
IN
OUT
IN
SW
×
(
)
=
)
-
V
LIR
I
R
RIPPLE
LOAD MAX
ESR
=
×
×
(
)
V
V
R
R
V
OUT
FB
C
D
RIPPLE
2
=
+
+
1
Integrated DDR Power-Supply Solution for
Desktops, Notebooks, and Graphic Cards
18
______________________________________________________________________________________
Figure 5. Dual-Mode Feedback Decoder
MAX8632
FB
0.1V
2.5V
(FIXED)
1.8V
(FIXED)
TO
ERROR
AMPLIFIER
REF (2.0V)
OUT