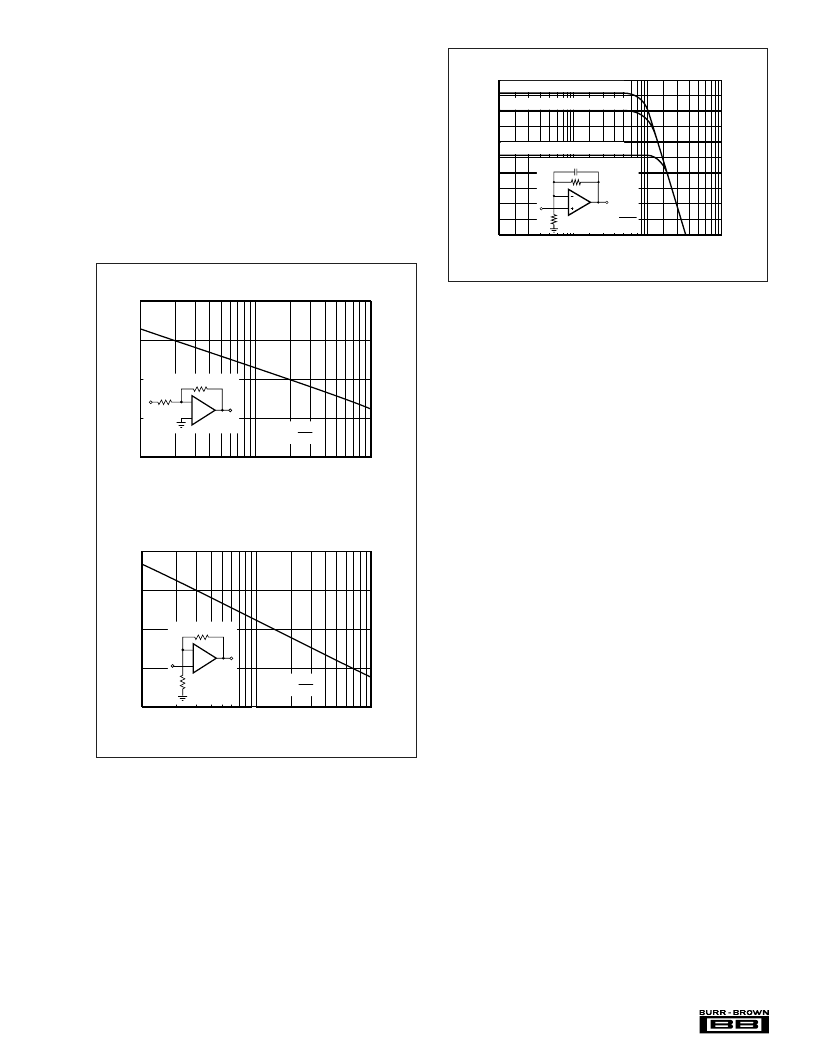
OPA603
11
R
F
(
) = 30 (30 – G) for V
S
=
±
15V
For example, for a gain of 10, use R
= 600
. Optimum
values differ slightly for
±
5V operation:
R
F
(
) = 30 (23 – G) for V
S
=
±
5V
C
will range from 1pF to 10pF depending on the selected
gain, load, and circuit layout. Adjust C
to optimize band-
width and minimize peaking. Figure 5 shows bandwidth
which can be acheived using this technique.
Typical values for this capacitor range from 1pF to 10pF
depending on closed-loop gain and load characteristics. Too
large a value of C
F
can cause instability.
FIGURE 5. Bandwidth Results with Added Capacitor C
F
.
VOLTAGE GAIN vs FREQUENCY
G = 20, R = 220 , C 8pF
V
30
20
10
0
–10
–20
1M
10M
100M
1G
Frequency (Hz)
G = 2, R = 820 , C 3pF
G = 10, R = 560 , C 3pF
R
I
R
F
C
F
R
F
R
I
G = 1 +
CIRCUIT LAYOUT
With any high-speed, wide-bandwidth circuitry, careful cir-
cuit layout will ensure best performance. Make short, direct
circuit interconnections and avoid stray wiring capacitance—
especially at the inverting input pin. A component-side
ground plane will help ensure low ground impedance. Do
not place the ground plane under or near the inputs and
feedback network.
Power supplies should be bypassed with good high-fre-
quency capacitors positioned close to the op amp pins. In
most cases, a 0.01
μ
F ceramic capacitor in parallel with a
2.2
μ
F solid tantalum capacitor at each power supply pin is
adequate. The OPA603 can deliver high load current—up to
150mA peak. Applications with low impedance or capaci-
tive loads demand large current transients from the power
supplies. It is the power supply bypass capacitors which
must supply these current transients. Larger bypass capaci-
tors such as 10
μ
F solid tantalum capacitors may improve
performance in these applications.
POWER DISSIPATION
High output current causes increased internal power dissipa-
tion in the OPA603. Copper leadframe construction maxi-
mizes heat dissipation compared to conventional plastic
packages. To achieve best heat dissipation, solder the device
directly to the circuit board and use wide circuit board
traces. Solder the unused pins, (1, 5 and 8) to a top-side
ground plane for improved power dissipation. Limit the load
and signal conditions depending on maximum ambient tem-
perature to assure operation within the power derating curve.
The OPA603 may be operated at reduced power supply
voltage to minimize power dissipation. Detailed specifica-
tions are provided for both
±
15V and
±
5V operation.
UNITY-GAIN OPERATION
As Figure 4b indicates, the OPA603 can be operated in unity
gain. A feedback resistor (approximately 2.8k
) sets the
appropriate open-loop characteristics and resistor R
is omit-
ted. Just as with gains greater than one, the value of the
feedback resistor (and capacitor if used) can be optimized
for the desired dynamic response and load characteristics.
Care should be exercised not to exceed the maximum differ-
ential input voltage rating of
±
6V. Large input voltage steps
which exceed the device’s slew rate of 1000V/
μ
s can apply
excessive differential input voltage.
FIGURE 4. Feedback Resistor Selection Curves.
BANDWIDTH AND FEEDBACK RESISTOR
vs INVERTING GAIN
Voltage Gain (V/V)
(4a)
–1
–10
–100
C
60
52.5
45
37.5
30
F
)
3k
2.25k
1.5k
750
0
+
–
R
F
R
I
G =–R
F
R
I
BANDWIDTH AND FEEDBACK RESISTOR
vs NONINVERTING GAIN
Voltage Gain (V/V)
(4b)
1
10
100
C
60
52.5
45
37.5
30
F
)
4k
3k
2k
1k
0
+
–
R
F
R
I
G = 1 +R
F
R
I