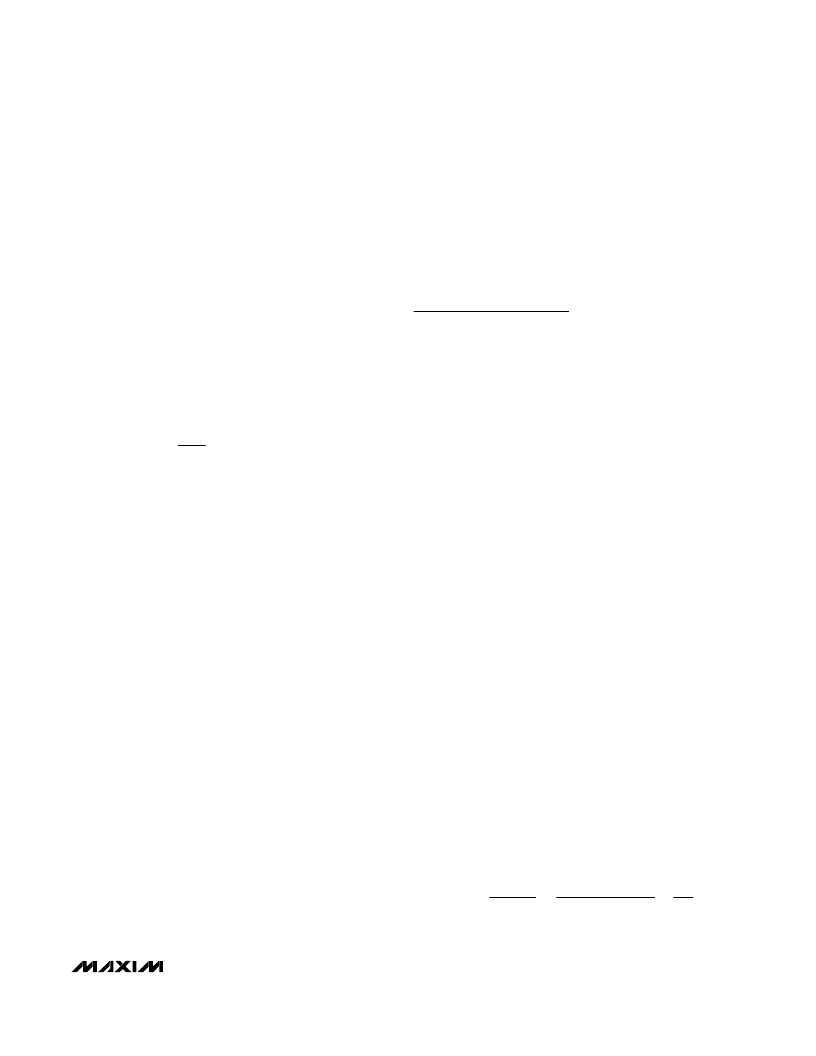
M
Quad-Output TFT LCD DC-DC
Converters with Buffer
______________________________________________________________________________________
25
where I
MAIN
includes the primary load current and the
input supply currents for the charge pumps (see
Charge-Pump
Input
Power
Considerations
), linear regulator, and VCOM buffer.
The linear regulator generates an output voltage by dis-
sipating power across an internal pass transistor, so
the power dissipation is simply the load current times
the input-to-output voltage differential:
and
Efficiency
When driving an external transistor, the internal linear
regulator provides the base drive current. Depending
on the external transistor
’
s current gain (
β
) and the
maximum load current, the power dissipated by the
internal linear regulator may still be significant:
The charge pumps provide regulated output voltages
by dissipating power in the low-side N-channel MOS-
FET, so they could be modeled as linear regulators fol-
lowed by unregulated charge pumps. Therefore, their
power dissipation is similar to a linear regulator:
[
=
(
where N is the number of charge-pump stages, V
DIODE
is the diodes
’
forward voltage, and V
SUPD
is the posi-
tive charge-pump diode supply (Figure 4).
The VCOM buffer
’
s power dissipation depends on the
capacitive load (C
LOAD
) being driven, the peak-to-
peak voltage change (V
P-P
) across the load, and the
load
’
s switching rate:
To find the total power dissipated in the device, the
power dissipated by each regulator and the buffer must
be added together:
The maximum allowed power dissipation is 975mW (24-
pin TSSOP) / 879mW (20-pin TSSOP) or:
P
MAX
= (T
J(MAX
) - T
A
) / (
θ
JB
+
θ
BA
)
where T
J
- T
A
is the temperature difference between
the controller
’
s junction and the surrounding air,
θ
JB
(or
θ
JC
) is the thermal resistance of the package to the
board, and
θ
BA
is the thermal resistance from the print-
ed circuit board to the surrounding air.
Design Procedure
Main Step-Up Converter
Output Voltage Selection
Adjust the output voltage by connecting a voltage-
divider from the output (VMAIN) to FB to GND (see
Typical Operating Circuit). Select R2 in the 10k
to
50k
range. Calculate R1 with the following equations:
R1 = R2 [(V
MAIN
/ V
REF
) - 1]
where V
REF
= 1.25V. V
MAIN
may range from V
IN
to 13V.
Inductor Selection
Inductor selection depends upon the minimum required
inductance value, saturation rating, series resistance, and
size. These factors influence the converter
’
s efficiency,
maximum output load capability, transient response time,
and output voltage ripple. For most applications, values
between 4.7μH and 22μH work best with the controller
’
s
switching frequency (Tables 1 and 2).
The inductor value depends on the maximum output
load the application must support, input voltage, output
voltage, and switching frequency. With high inductor
values, the MAX1778/MAX1880
–
MAX1885 source high-
er output currents, have less output ripple, and enter
continuous conduction operation with lighter loads;
however, the circuit
’
s transient response time is slower.
On the other hand, low-value inductors respond faster
to transients, remain in discontinuous conduction oper-
ation, and typically offer smaller physical size for a
given series resistance and current rating. The equa-
tions provided here include a constant LIR, which is the
ratio of the peak-to-peak AC inductor current to the
average DC inductor current. For a good compromise
between the size of the inductor, power loss, and out-
put voltage ripple, select an LIR of 0.3 to 0.5. The
inductance value is then given by:
L
V
V
V
V
I
LIR
MIN
IN MIN
(
MAIN
MAIN
IN MIN
(
MAIN MAX OSC
(
-
)
)
)
=
2
1
η
P
P
+
P
P
P
P
TOTAL
STEP UP
LDO INT
+
NEG
POS
BUF
+
+
(
)
=
-
P
V
BUF
P
P LOAD LOAD SUPB
-
=
P
I
V
V
N
)
)
V
P
I
V
V
N
V
V
NEG
NEG
SUPN
DIODE
NEG
POS
POS
SUPP
DIODE
SUPD
POS
-
-
-
+
-
=
(
[
]
]
2
2
P
I
V
V
V
I
V
V
LDO INT
LDO
β
SUPL
LDO
LDOOUT
SUPL
LDOOUT
(
)
-
0 7
(
-
)
=
(
)
[
]
=
P
I
V
V
LDO INT
LDO
SUPL
LDO
(
)
(
-
)
=