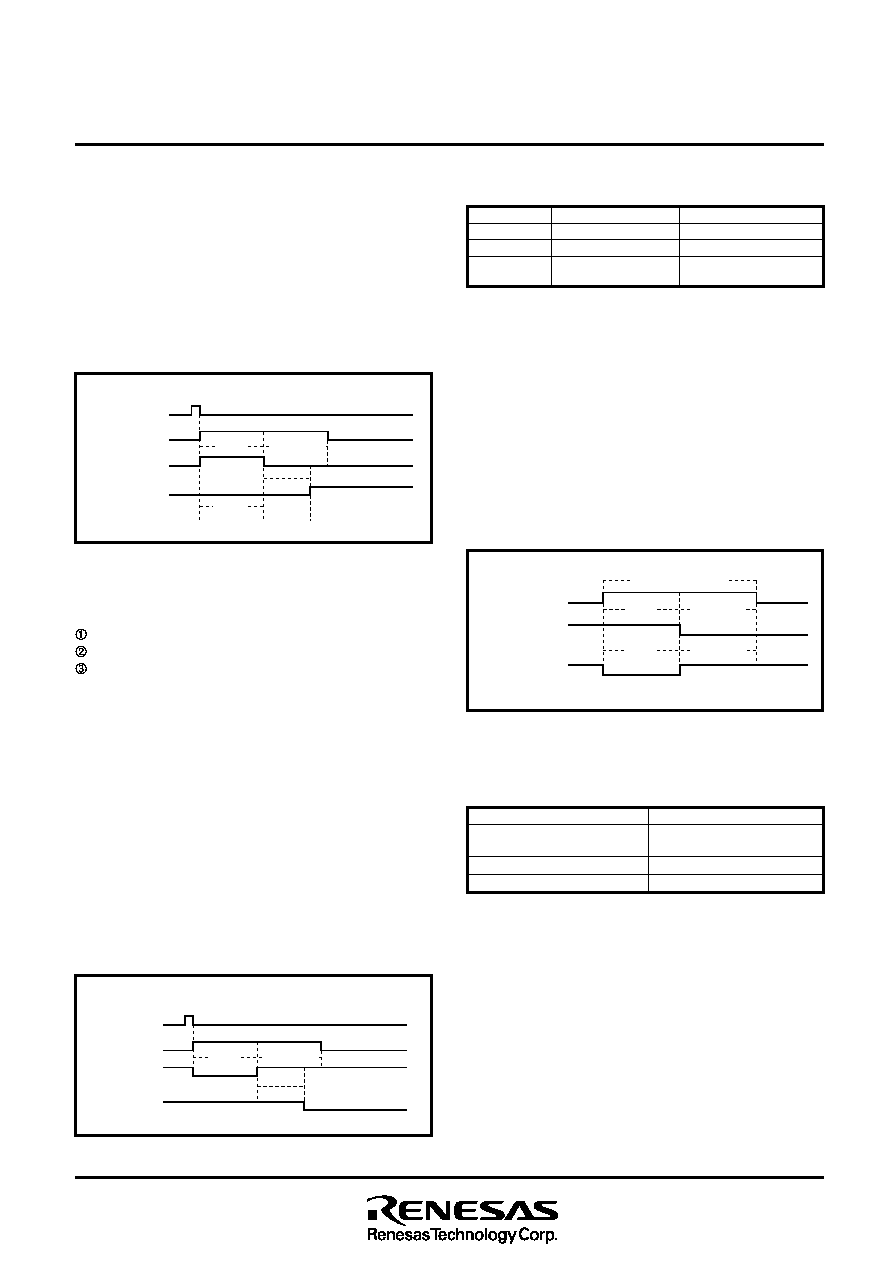
36
MITSUBISHI MICROCOMPUTERS
M37207MF-XXXSP/FP, M37207M8-XXXSP
M37207EFSP/FP
SINGLE-CHIP 8-BIT CMOS MICROCOMPUTER for VOLTAGE SYNTHESIZER
and ON-SCREEN DISPLAY CONTROLLER
(9) START/STOP Condition Detect Conditions
The START/STOP condition detect conditions are shown in
Figure 33 and Table 4. Only when the 3 conditions of Table 4 are
satisfied, a START/STOP condition can be detected.
Note: When a STOP condition is detected in the slave mode
(MST = 0), an interrupt request signal “IICIRQ” is generated
to the CPU.
(8) STOP Condition Generation Method
When the ES0 bit of the I2C control register (address 00DC16) is “1,”
execute a write instruction to the I2C status register (address 00DB16)
for setting the MST bit and the TRX bit to “1” and the BB bit to “0”. A
STOP condition will then be generated. The STOP condition genera-
tion timing and the BB flag reset timing are different in the standard
clock mode and the high-speed clock mode. Refer to Figure 32 for
the STOP condition generation timing diagram, and Table 3 for the
START condition/STOP condition generation timing table.
Fig. 32. STOP Condition Generation Timing Diagram
Fig. 33. START Condition/STOP Condition Detect Timing
Diagram
Table 4. START Condition/STOP Condition Detect Conditions
Table 3. START Condition/STOP Condition Generation Timing
Table
Item
Setup time
Hold time
Set/reset time
for BB flag
Standard Clock Mode
5.0 s (20 cycles)
3.0 s (12 cycles)
High-speed Clock Mode
2.5 s (10 cycles)
1.5 s (6 cycles)
Note: Absolute time at
φ = 4 MHz. The value in parentheses de-
notes the number of
φ cycles.
I2C status register
write signal
Reset time for
BB flag
Hold time
Setup
time
SCL
SDA
BB flag
Hold time
Setup
time
SCL
SDA
(START condition)
SDA
(STOP condition)
SCL release time
Hold time
Setup
time
(6) START Condition Generation Method
When the ESO bit of the I2C control register (address 00DC16) is “1,”
execute a write instruction to the I2C status register (address 00DB16)
to set the MST, TRX and BB bits to “1.” A START condition will then
be generated. After that, the bit counter becomes “0002” and an SCL
for 1 byte is output. The START condition generation timing and BB
bit set timing are different in the standard clock mode and the high-
speed clock mode. Refer to Figure 31 for the START condition gen-
eration timing diagram, and Table 3 for the START condition/STOP
condition generation timing table.
Fig. 31. START Condition Generation Timing Diagram
(7) RESTART Condition Generation Method
To generate the RESTART condition, take the following sequence:
Set “2016” to the I2C status register (S1).
Write a transmit data to the I2C data shift register.
Set “F016” to the I2C status register (S1) again.
<Example of Setting of RESTART Condition>
I2C status register
; S1 = 2016
I2C data shift register ; S0 = transmit data after restart
I2C status register
; S1 = F016
I2C status register
write signal
Set time for
BB flag
Hold time
Setup
time
SCL
SDA
BB flag
Setup
time
Standard Clock Mode
6.5 s (26 cycles) < SCL
release time
3.25 s (13 cycles) < Setup time
3.25 s (13 cycles) < Hold time
High-speed Clock Mode
1.0 s (4 cycles) < SCL
release time
0.5 s (2 cycles) < Setup time
0.5 s (2 cycles) < Hold time
Note: Absolute time at
φ = 4 MHz. The value in parentheses de-
notes the number of
φ cycles.