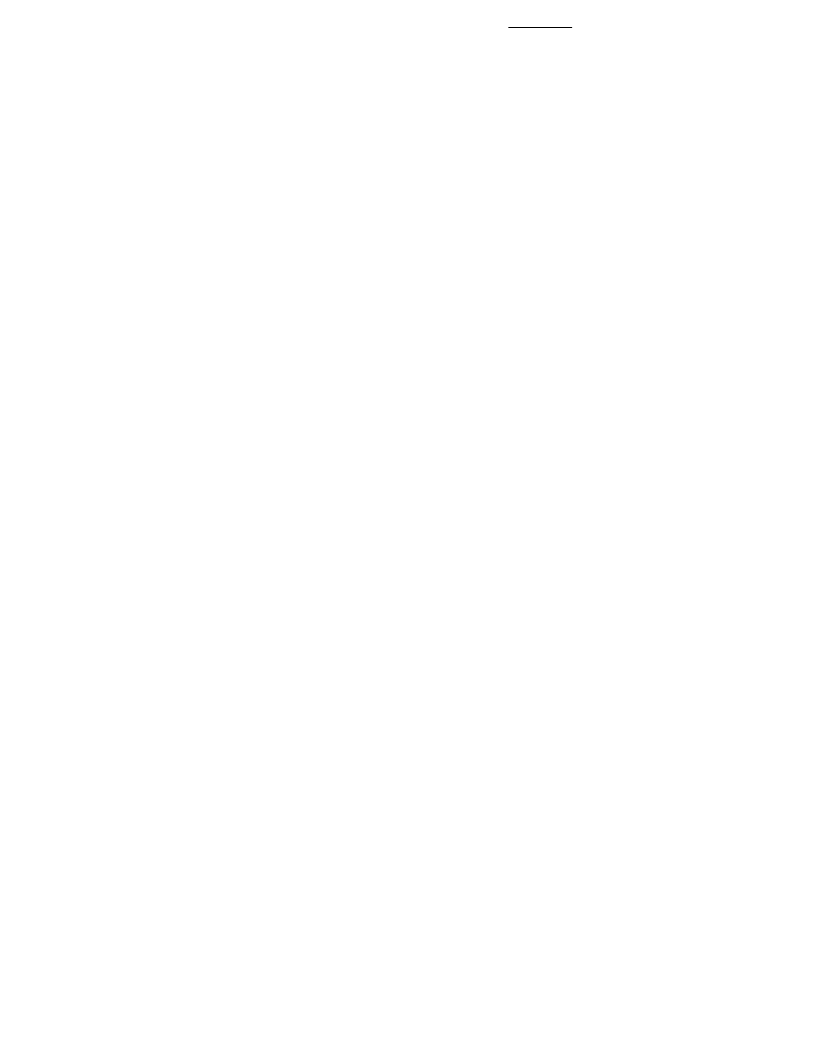
5
Electromagnetic
Interference (EMI)
One of a circuit board designer’s
foremost concerns is the control
of electromagnetic emissions
from electronic equipment.
Success in controlling generated
Electromagnetic Interference
(EMI) enables the designer to
pass a governmental agency’s
EMI regulatory standard; and
more importantly, it reduces the
possibility of interference to
neighboring equipment. There are
three options available for the
HFCT-5218M with regard to EMI
shielding for providing the
designer with a means to achieve
good EMI performance. The EMI
performance of an enclosure
using these transceivers is
dependent on the chassis design.
Agilent encourages using
standard RF suppression
practices and avoiding poorly
EMI-sealed enclosures. In
addition, Agilent advises that for
the best EMI performance, the
metalized case must be
connected to chassis ground
using one of the shield options.
An un-shielded option, shown in
Figure 6 is available for the
HFCT-5218M fiber optic
transceiver. This unit is intended
for applications where EMI is
either not an issue for the
designer, or the unit resides in a
highly-shielded enclosure.
The first shielded option, option
EM, is for applications where the
position of the transceiver
module will extend outside the
equipment enclosure. The
metallized plastic package and
integral external metal shield of
the transceiver helps locally to
terminate EM fields to the chassis
to prevent their emissions outside
the enclosure. This metal shield
contacts the panel or enclosure
on the inside of the aperture on
all but the bottom side of the
shield and provides a good RF
connection to the panel. This
option can accommodate various
panel or enclosure thicknesses,
i.e. 1.02 mm (.04 in) min to
2.54 mm (0.1 in) max. The
reference plane for this panel
thickness variation is from the
front surface of the panel or
enclosure. The recommended
length for protruding the
HFCT-5218EM transceiver beyond
the front surface of the panel or
enclosure is 6.35 mm (0.25 in) .
With this option, there is
flexibility of positioning the
module to fit the specific need of
the enclosure design. (See Figure
7 for the mechanical drawing
dimensions of this shield.)
The second shielded option,
option FM, is for applications
that are designed to have a flush
mounting of the module with
respect to the front of the panel or
enclosure. The flush-mount design
accommodates a large variety of
panel thickness, i.e. 1.02 mm
(.04 in) min to 2.54 mm (0.1 in)
max. Note the reference plane for
the flush-mount design is the
interior side of the panel or
enclosure. The recommended
distance from the centerline of
the transceiver front solder posts
to the inside wall of the panel is
13.82 mm (0.544 in) . This option
contacts the inside panel or
enclosure wall on all four sides
of this metal shield. (See Figure 8
for the mechanical drawing
dimensions of this shield.)
Both shielded design options
connect only to the equipment
chassis and not to the signal or
logic ground of the circuit board
within the equipment closure.
The front panel aperture
dimensions are recommended in
Figures 9 and 10. When layout of
the printed circuit board is done to
incorporate these metal-shielded
transceivers, keep the area on the
printed circuit board directly
under the external metal shield
free of any components and
circuit board traces. For
additional EMI performance
advantage, use duplex SC fiber-
optic connectors that have low
metal content inside the
connector. This lowers the ability
of the metal fiber-optic
connectors to couple EMI out
through the aperture of the panel
or enclosure.