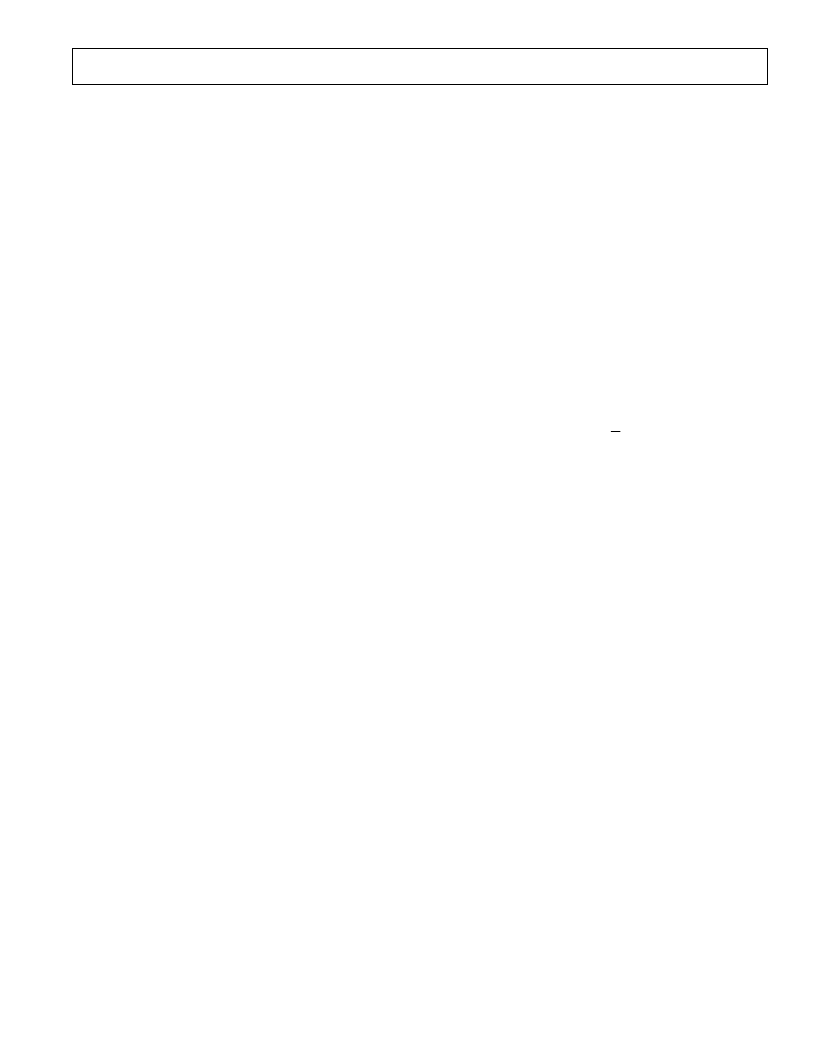
ADDC02812DA/ADDC02815DA
REV. A
–11–
Input Voltage T ransient Protection
: T he converters have a
transient voltage suppressor connected across their input leads
to protect the units against high voltage pulses (both positive
and negative) of short duration. With the power supply con-
nected in the typical system setup shown in Figure 17, a tran-
sient voltage pulse is created across the converter in the
following manner. A 20
μ
F capacitor is first charged to 400 V.
It is then connected directly across the converter’s end of the
two meter power lead cable through a 2
on-state resistance
MOSFET . T he duration of this connection is 10
μ
s. T he pulse
is repeated every second for 30 minutes. T his test is repeated
with the connection of the 20
μ
F capacitor reversed to create a
negative pulse on the supply leads. (If continuous reverse volt-
age protection is required, a diode can be added externally in
series at the expense of lower efficiency for the power system.)
T he converter responds to this input transient voltage test by
shutting down due to its input overvoltage protection feature.
Once the pulse is over, the converter initiates a soft-start, which
is completed before the next pulse. No degradation of converter
performance occurs.
T HE RMAL CHARACT E RIST ICS
Junction and Case T emperatures
: It is important for the
user to know how hot the hottest semiconductor junctions
within the converter get and to understand the relationship
between junction, case, and ambient temperatures. T he hottest
semiconductors in the 100 W product line of Analog Devices’
high density power supplies are the switching MOSFET s and
the output rectifiers. T here is an area inside the main power
transformers that is hotter than these semiconductors, but it is
within NAVMAT guidelines and well below the Curie tempera-
ture of the ferrite. (T he Curie temperature is the point at which
the ferrite begins to lose its magnetic properties.)
Since NAVMAT guidelines require that the maximum junction
temperature be 110
°
C, the power supply manufacturer must
specify the temperature rise above the case for the hottest semi-
conductors so the user can determine what case temperature is
required to meet NAVMAT guidelines. T he thermal charac-
teristics section of the specification table states the hottest junc-
tion temperature for maximum output power at a specified case
temperature. T he unit can operate to higher case temperatures
than 90
°
C, but 90
°
C is the maximum temperature that permits
NAVMAT guidelines to be met.
Case and Ambient T emperatures
: It is the user’s responsi-
bility to properly heat sink the power supply in order to maintain
the appropriate case temperature and, in turn, the maximum
junction temperature. Maintaining the appropriate case tem-
perature is a function of the ambient temperature and the
mechanical heat removal system. T he static relationship of
these variables is established by the following formula:
T
C
= T
A
+
(
P
D
×
R
θ
CA
)
where
T
C
=
case temperature measured at the center of the package
bottom,
T
A
=
ambient temperature of the air available for cooling,
P
D
=
the power, in watts, dissipated in the power supply,
R
θ
CA
=
the thermal resistance from the center of the package
to free air, or case to ambient.
T he power dissipated in the power supply,
P
D
, can be calculated
from the efficiency,
h
, given in the data sheets and the actual
output power,
P
O
, in the user’s application by the following
formula:
P
D
=
P
O
1
η
±1
For example, at 80 W of output power and 80% efficiency, the
power dissipated in the power supply is 20 W. If under these
conditions, the user wants to maintain NAVMAT deratings
(i.e., a case temperature of approximately 90
°
C) with an ambi-
ent temperature of 75
°
C, the required thermal resistance, case
to ambient, can be calculated as
90
=
75
+
(20
×
R
θ
CA
)
or
R
θ
CA
=
0.75
°
C/W
T his thermal resistance, case to ambient, will determine what
kind of heat sink and whether convection cooling or forced air
cooling is required to meet the constraints of the system.
SY ST E M INST ABILIT Y CONSIDE RAT IONS
In a distributed power supply architecture, a power source
provides power to many “point-of-load” (POL) converters. At
low frequencies, the POL converters appear incrementally as
negative
resistance loads. T his negative resistance could cause
system instability problems.