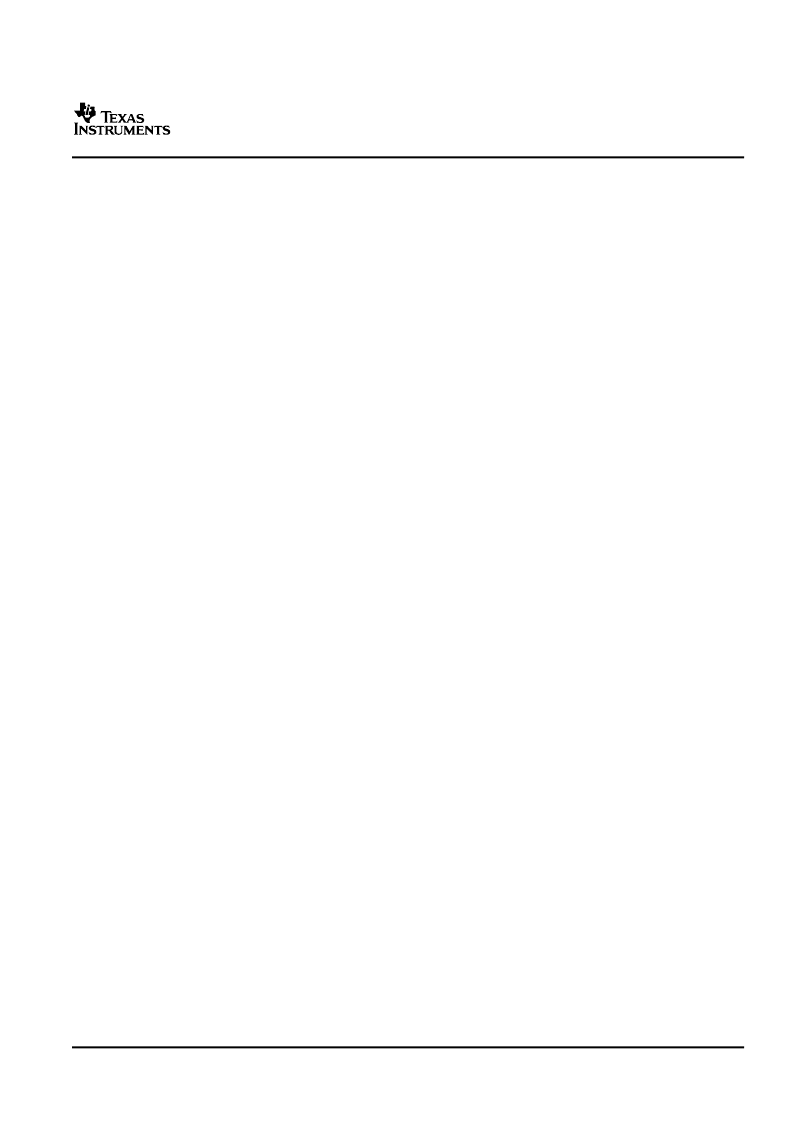
www.ti.com
DETAILED DESCRIPTION
OPERATION
The TPS61058/9 familly is based on a fixed frequency multiple feedforward controller topology. Input voltage,
output voltage, and voltage drop on the NMOS switch are monitored and forwarded to the regulator. So changes
in the operating conditions of the converter directly affect the duty cycle and must not take the indirect and slow
way through the control loop and the error amplifier.
Synchronous Rectifier
Down Regulation
Enable
TPS61058
TPS61059
SLVS572B–APRIL 2005–REVISED DECEMBER 2005
The control loop, determined by the error amplifier, only has to handle small signal errors. The input for it is the
feedback voltage on the FB pin. It is compared with the internal reference voltage to generate an accurate and
stable LED current.
The peak current of the NMOS switch is also sensed to limit the maximum current flowing through the switch and
the inductor. The typical peak current limit is set to 1000mA (TPS61058) and 1500 mA (TPS61059). An internal
temperature sensor prevents the device from getting overheated in case of excessive power dissipation.
The device integrates an N-channel and a P-channel MOSFET transistor to realize a synchronous rectifier.
Because the commonly used discrete Schottky rectifier is replaced with a low RDS(ON) PMOS switch, the power
conversion stage itself can reach 96% efficiency.
In order to avoid ground shift due to the high currents in the NMOS switch, two separate ground pins are used.
The reference for all control functions is the GND pin. The source of the NMOS switch is connected to PGND.
Both grounds must be connected on the PCB at only one point close to the GND pin.
A special circuit is applied to disconnect the load from the input during shutdown of the converter. In conventional
synchronous rectifier circuits, the backgate diode of the high-side PMOS is forward biased in shutdown and
allows current flow from the battery to the output. This device however uses a special circuit which takes the
cathode of the backgate diode of the high-side PMOS and disconnects it from the source when the regulator is
not enabled (EN = Low).
The benefit of this feature for the system design engineer is that the battery is not depleted during shutdown of
the converter. No additional components have to be added to the design to make sure that the battery is
disconnected from the output of the converter.
In general, a boost converter only regulates output voltages which are higher than the input voltage. This device
operates differently and is capable of driving high power single die white LEDs from a fully charged Li-Ion cell. To
control this applications properly, a down conversion mode is implemented.
If the input voltage reaches or exceeds the output voltage necessary to maintain the LED current within
regulation, the converter changes to a down conversion mode. In this mode, the control circuit changes the
behavior of the rectifying PMOS transitor. It sets the voltage drop across the PMOS as high as needed to
regulate the output voltage. This means the power losses in the converter increase. This has to be taken into
account for thermal consideration especially when operating with low V
F
LEDs, high battery voltages and high
LED currents.
The device is put into operation when EN is set high. It is put into a shutdown mode when EN is set to GND. The
EN input pin has an internal 400-k
pull-down resistor to disable the device when this pin is floating.
In shutdown mode, the regulator stops switching, the internal control circuitry is switched off, and the load is
isolated from the input (as described in the Synchronous Rectifier Section). This also means that the output
voltage can drop below the input voltage during shutdown.
11