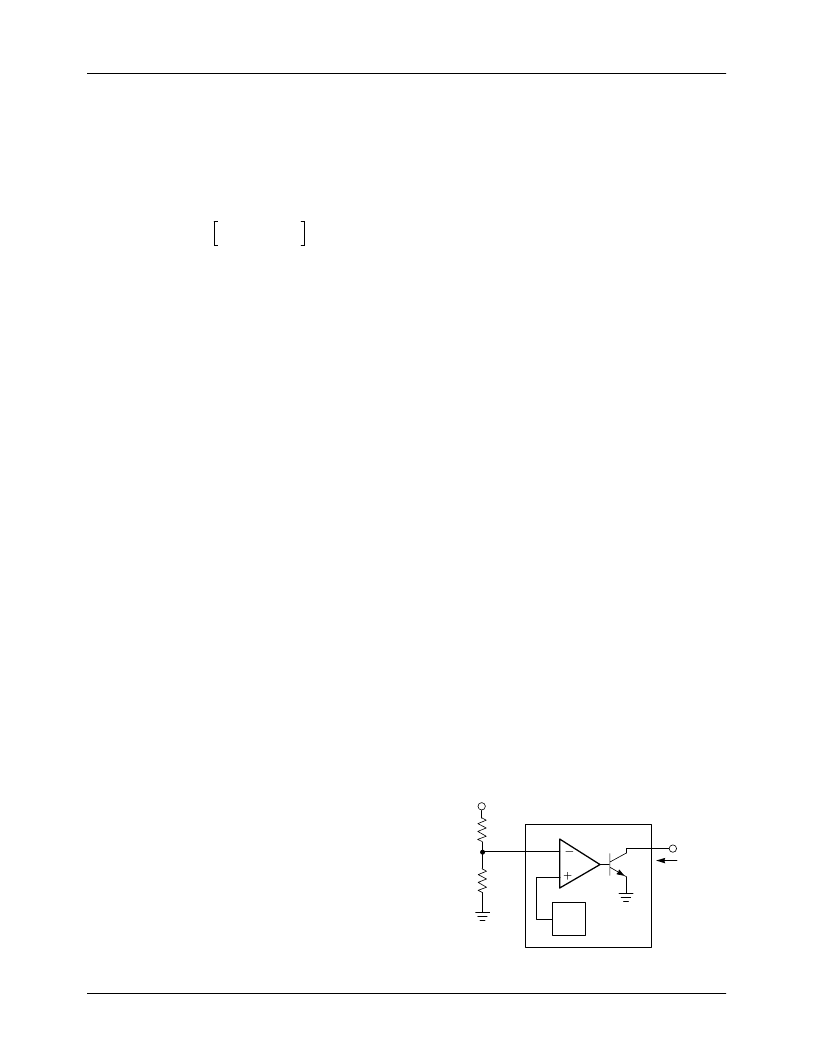
PRODUCT SPECIFICATION
RC4391
10
Step-Down Design Procedure
1. Select an operating frequency.
2. Determine the maximum on time T
ON
as in the inverting
design procedure.
3. Calculate I
MAX
:
4. Calculate L
X
:
Alternate Design Procedure
The design equations above will not work for certain input/
output voltage ratios, and for these circuits another method
of defining component values must be used. If the slope of
the current discharge waveform is much less than the slope
of the current charging waveform, then the inductor current
will become continuous (never discharging completely), and
the equations will become extremely complex. So, if the
voltage applied across the inductor during the charge time is
greater than during the discharge time, use the design proce-
dure below. For example, a step-down circuit with 20V input
and 5V output will have approximately 15V across the
inductor when charging, and approximately 5V when dis-
charging. So in this example the inductor current will be con-
tinuous and the alternate procedure will be necessary. The
alternate procedure may also be used for discontinuous cir-
cuits.
1. Select an operating frequency based on efficiency and
component size requirements (a value between 10kHz
and 50kHz is typical).
2. Build the circuit and apply the worst case conditions to
it, i.e., the lowest battery voltage and the highest load
current at the desired output voltage.
3. Adjust the inductor value down until the desired output
voltage is achieved, then decrease its value by 30% to
cover manufacturing tolerances.
4. Check the output voltage with an oscilloscope for ripple,
at high supply voltages, at voltages as high as are
expected. Also check for efficiency by monitoring supply
and output voltages and currents:
5. If the efficiency is poor, go back to Step 1 and start over.
If the ripple is excessive, then increase the output filter
capacitor value or start over.
I
MAX
2I
V
OUT
F
O
(
)
T
ON
(
)
OUT
V
D
–
(
)
)
----------–
1
+
----------------------------------V
=
L
X
(Henries)
V
----I
V
–
MAX
è
T
ON
(
)
=
eff
V
S
)
I
OUT
(
)
I
SY
(
)
(
)
x100
-+V
=
è
Compensation
When large values (> 50 k
W
) are used for the voltage setting
resistors (R1 and R2 of Figure 8) stray capacitance at the
V
FB
input can add lag to the feedback response, destabiliz-
ing the regulator, increasing low frequency ripple, and lower-
ing efficiency. This can often be avoided by minimizing the
stray capacitance at the V
FB
node. It can also be remedied by
adding a lead compensation capacitor of 100 pF to 10 nF. In
inverting applications, the capacitor connects between
-V
OUT
and V
FB
; for step-down circuits it connects between
ground and V
FB
. Most applications do not require this
capacitor.
Inductors
Efficiency and load regulation will improve if a quality high
Q inductor is used. A ferrite pot core is recommended; the
wind-yourself type with an air gap adjustable by washers or
spacers is very useful for bread-boarding prototypes. Care
must be taken to choose a core with enough permeability to
handle the magnetic flux produced at I
MAX
. If the core satu-
rates, then efficiency and output current capability are
severely degraded and excessive current will flow through
the switch transistor. A pot core inductor design section is
provided later in this datasheet.
An isolated AC current probe for an oscilloscope (example:
Tektronix P6042) is an excellent tool for saturation prob-
lems; with it the inductor current can be monitored for non-
linearity at the peaks (a sign of saturation).
Low Battery Detector
An open collector signal transistor Q2 with comparator C2
provides the designer with a method of signaling a display or
computer whenever the battery voltage falls below a pro-
grammed level (see Figure 13). This level is determined by
the +1.25V reference level and by the selection of two exter-
nal resistors according to the equation:
When the battery drops below this threshold Q2 will turn on
and sink typically 600
m
A. The low battery detection circuit
can also be used for other less conventional applications such
as the voltage dependent oscillator circuit of Figure 18.
Figure 13. Low Battery Detector
V
TH
V
REF
R5
R4
1
+
è
=
+Vs
R4
R5
1
C2
V
1.25V
Q2
2
I
LBD
65-1651A
LBR
LBD