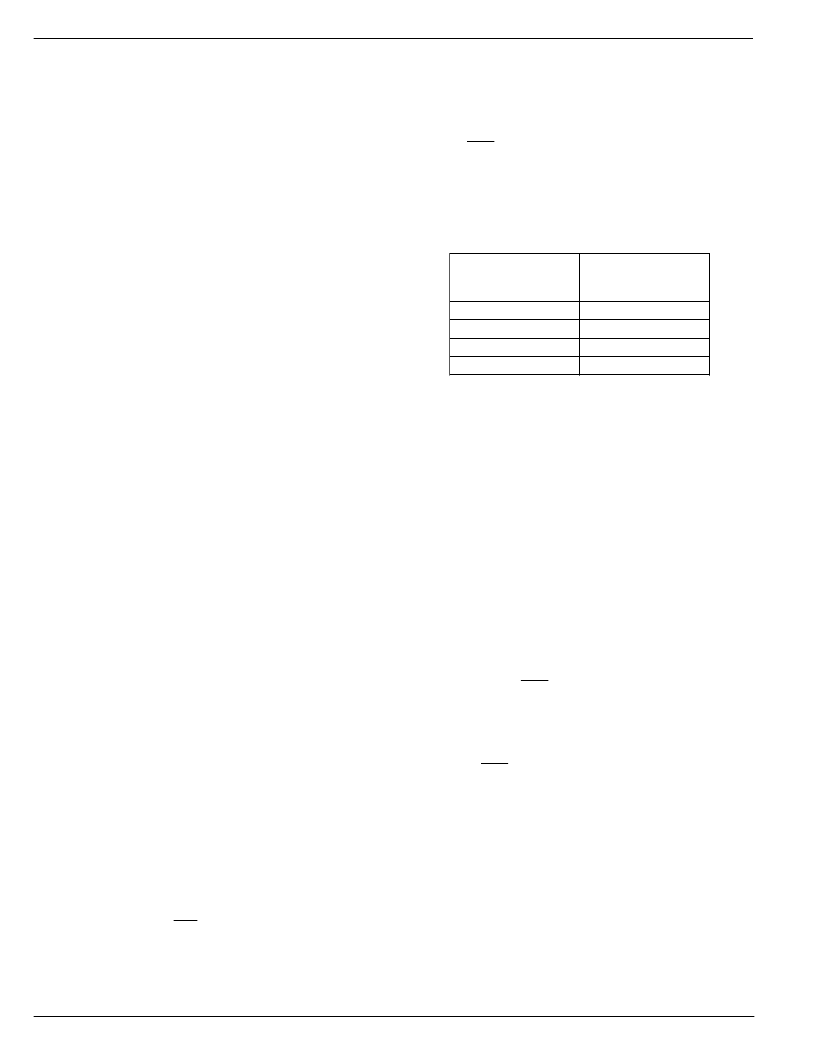
MICRF007
Application Information
Transmitter Compatibility
Generally, best performance and range will be realized when
the MICRF007 is operated in a system using a SAW or crystal
based transmitter. The receiver reference oscillator requires
the use of a crystal.
Bypass Capacitors
The power supply bypass capacitors connected to VDD
should have the shortest possible lead lengths. For best
performance, connect directly to VSS
Optional BandPass Filter
For applications located in high ambient noise environments,
a fixed value band-pass network may be connected between
the ANT pin and VSS to provide additional receive selectivity
and input overload protection. A typical filter is included in
Figure 7a.
Data Squelching
During quiet periods (no signal) the data output (DO pin)
transitions randomly with noise, presenting problems for
some decoders. A simple solution is to introduce a small
offset, or squelch voltage, on the CTH pin so that noise does
not trigger the internal comparator. Usually 20mV to 30mV is
sufficient, and may be introduced by connecting a several-
megohm resistor from the CTH pin to either V
SS
or V
DD
,
depending on the desired offset polarity. Since the MICRF007
has receiver AGC, noise at the internal comparator input is
always the same, set by the AGC. The squelch offset require-
ment does not change as the local noise strength changes
from installation to installation. Introducing squelch will re-
duce range modestly. Only introduce an amount of offset
sufficient to quiet the output.
AGC Configuration
By adding resistance from the CAGC pin to VDDBB or
VSSBB in parallel with the AGC capacitor, the ratio of decay-
to-attack time constant may be varied, although the value of
such adjustments must be studied on a per-application basis.
Generally the design value of 10:1 is adequate for the vast
majority of applications.
To maximize system range, it is important to keep the AGC
control voltage ripple low, preferably under 10mVpp once the
control voltage has attained its quiescent value. For this
reason capacitor values of at least 0.47
μ
F are recommended.
Crystal Selection
Selecting Reference Oscillator Frequency f
T
As with any superheterodyne receiver, the difference be-
tween the internal LO (local oscillator) frequency f
LO
and the
incoming transmit frequency f
TX
ideally must equal the IF
center frequency. Equation 1 may be used to compute the
appropriate f
LO
for a given f
TX
:
Micrel
MICRF007
12
December 2000
(1)
f
f
1.064f
390
LO
TX
TX
=
±
Frequencies f
TX
and f
LO
are in MHz. Note that two values of
f
LO
exist for any given f
TX
, distinguished as
“
high-side mixing
”
and
“
low-side mixing,
”
and there is generally no preference of
one over the other.
After choosing one of the two acceptable values of f
LO
, use
Equation 2 to compute the reference oscillator frequency f
T
:
f
64.5
Frequency f
T
is in MHz. Connect a crystal of frequency f
T
to
REFOSC on the MICRF007. Four-decimal-place accuracy
on the frequency is generally adequate. The following table
identifies f
T
for some common transmit frequencies.
(2)
f
T
LO
=
t
c
m
n
e
s
n
u
q
f
X
T
M
5
1
0
9
8
1
4
9
3
a
r
e
T
r
y
F
r
o
t
s
y
c
n
O
e
e
u
q
f
T
7
9
3
6
8
9
5
4
c
n
e
r
e
F
r
e
R
z
z
z
H
H
H
H
M
3
3
z
z
z
z
H
H
H
H
M
M
M
M
0
0
3
8
8
0
4
7
M
M
2
z
4
Table 2. Common Transmitter Frequencies
External Timing Signals
Externally applied signals should be ac-coupled and the
amplitude must be limited to approximately 0.5Vpp.
Frequency and Capacitor Selection
Selection of the slicing level capacitor (C
TH
), and AGC
capacitor (C
AGC
) are briefly summarized in this section.
Selecting Capacitor C
TH
The first step in the process is selection of a data-slicing-level
time constant. This selection is strongly dependent on sys-
tem issues including system decode response time and data
code structure (that is, existence of data preamble, etc.). This
issue is covered in more detail in Application Note 22.
Source impedance of the CTH pin is given by equation (4),
where f
T
is in MHz:
4.90
f
T
Assuming that a slicing level time constant
τ
has been
established, capacitor C
TH
may be computed using equation
τ
(4)
R
1
k
SC
=
18
(5)
C
R
TH
SC
=
A standard
±
20% X7R ceramic capacitor is generally suffi-
cient.
Selecting C
AGC
Capacitor in Continuous Mode
Selection of C
AGC
is dictated by minimizing the ripple on the
AGC control voltage by using a sufficiently large capacitor.
Factory experience suggests that C
AGC
should be in the
vicinity of 0.47
μ
F to 4.7
μ
F. Large capacitor values should be
carefully considered as this determines the time required for
the AGC control voltage to settle from a completely dis-
charged condition. AGC settling time from a completely
discharged (zero-volt) state is given approximately by Equa-
tion 6: