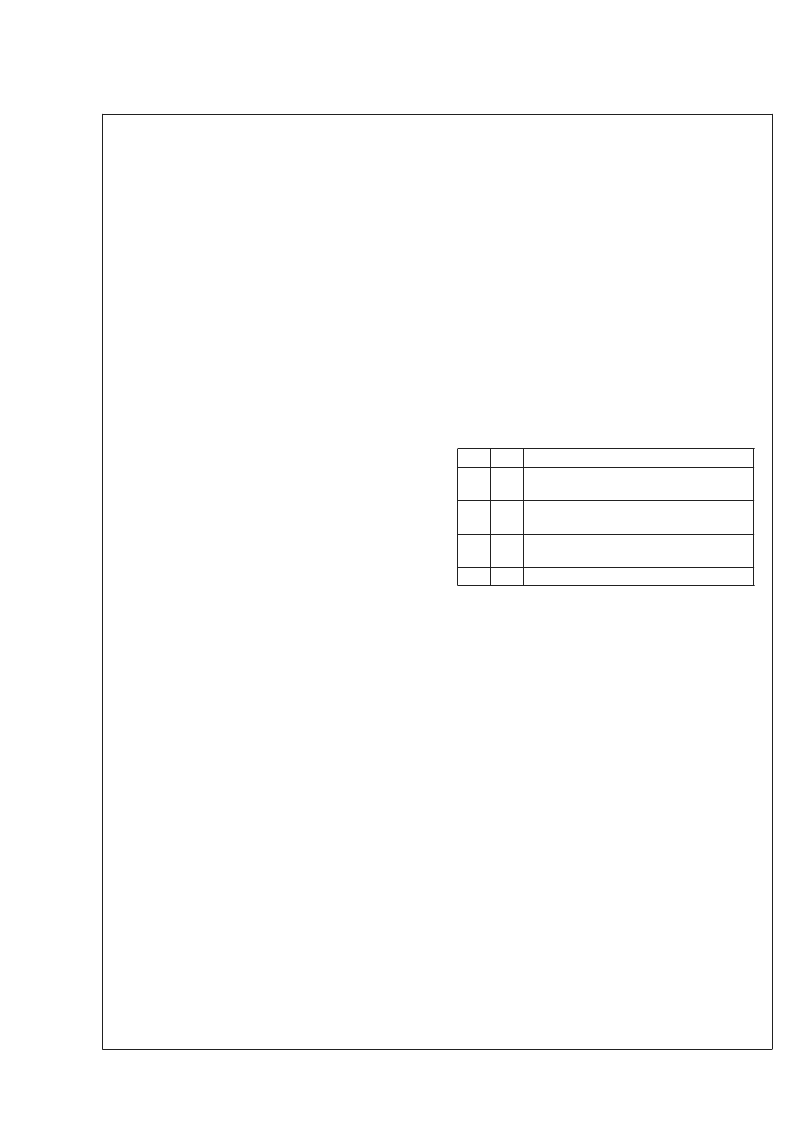
Application Information
(Continued)
important to provide a large heat spreading pad on the
opposite side of the board. The vias will provide a good
thermal connection between the pad under the IC, and the
heat spreading pad on the bottom of the board. Thermal
modelling can be done using the
θ
junction to pad informa-
tion provided, to calculate the required area of copper based
on the ambient temperature of the system, and the calcu-
lated amount of thermal dissipation in the LM98555.
POWER DISSIPATION
The amount of power dissipated in the device can be deter-
mined by considering the following factors:
Power dissipated delivering energy to the load capaci-
tance
Power dissipated delivering energy to parasitic capaci-
tance
Power dissipated due to leakage in the IC
The amount of power dissipated due to leakage is very small
in this CMOS device. Most of the power will be due to the
load capacitance being switched, with a small additional
amount caused by the parasitic capacitance of the output
circuitry, output pins, and PCB traces. A typical parasitic
capacitance would be on the order of 5 pF. Since the load
capacitance will be on the order of 100 pF or more, this
usually dominates the power dissipation calculation. The
following equation can be used to calculate the power dissi-
pation due to capacitive switching of the loads:
P = Sum[Output Frequency x Load Capacitance x Output
Voltage Squared] (summed for all outputs)
INPUT SIGNALS
Care should be taken to match the trace lengths between
timing signals that require low skew. Usually, the P1A and
P2A signals will be the most critical. In some applications,
the timing of P2B with respect to P1A and P2A can also be
important, and that input trace should also be carefully de-
signed.
Trace shape and width should also be carefully controlled.
The trace geometry will determine the characteristic imped-
ance of each trace. The impedance should be set to give
reasonable immunity to noise coupling into the trace. With a
known trace impedance, the signals can be terminated using
a series resistor at the source that is equal to the character-
istic impedance. This will provide a signal with minimum
overshoot and ringing, and will contribute to better perfor-
mance of the final signal reaching the CCD.
OUTPUT CONNECTIONS AND LOADING EXAMPLES
The LM98555 can be used with a wide variety of different
CCD sensors. The P1Aoutx and P2Aoutx outputs can be
selectively enabled to provide 2, 4, 6, or 8 drivers. This
allows the available drive strength to be optimized for the
sensor and application. Connecting multiple outputs together
in parallel as shown in the typical application circuit provides
lower drive impedance as needed to suit the load being
driven. When driving smaller loads, lower switching noise
will be generated if the minimum necessary outputs are
enabled and used.
The output signal traces should also be designed for a
known impedance. Source terminating resistors should be
used in series with each output to provide good matching to
the trace characteristic impedance. The resistors should be
located as close as possible to each output pin. If multiple
outputs will be combined to drive a single load pin, the output
signals should be combined after the termination resistors.
This will provide the best summing of adjacent outputs. The
combined signal should then pass through an EMI type
ferrite bead. This component can be selected to change the
bandwidth or shape of the clocking signal to achieve the best
CCD transfer efficiency.
Several other techniques will also help maintain signal qual-
ity, and minimize timing differences between critical signals.
Vias should not be used for critical timing signals. These can
add impedance discontinuities that will affect the waveform
quality. Traces should have gradual bends and avoid sharp
changes in direction that can also introduce impedance dis-
continuities.
SELECTIVE DRIVER ENABLING
With the Enable pins, the user has the capability to enable
only the drivers that are required for the application, thus
eliminating unnecessary outputs switching. The following
table shows the details.
EN1
0
EN0
0
Driver-set State
P1Aout(1:0) and P2Aout(1:0) are enabled;
all others disabled.
P1Aout(3:0) and P2Aout(3:0) are enabled;
all others disabled.
P1Aout(5:0) and P2Aout(5:0) are enabled;
all others disabled.
All P1Aout and P2Aout drivers are enabled.
Note: The disabled drivers’ outputs are in TRI-STATE.
0
1
1
0
1
1
POWER AND GROUND - PLANES VERSUS BUSES
The best performance will be achieved by using planes
rather than traces for power and ground. Planes provide
lower electrical and thermal impedance. Ground bounce and
ringing are reduced, electromagnetic emissions are mini-
mized and the best thermal performance will be realized.
A single common ground plane should be used for all power
and signal domains.
Another circuit board layer can be used to provide power to
the various circuitry. Different power buses can be provided
by isolated planes within this layer of the circuit board.
EMI MANAGEMENT
Good EMI control will be achieved by addressing the follow-
ing items:
Provide proper source termination of output signals
Limit length of output traces
Ensure adequate power supply decoupling
Provide power and ground planes as much as possible
Provide common ground plane for all signals, especially
between LM98555 outputs and load CCD
Enable and use the minimum number of outputs needed
L
www.national.com
8