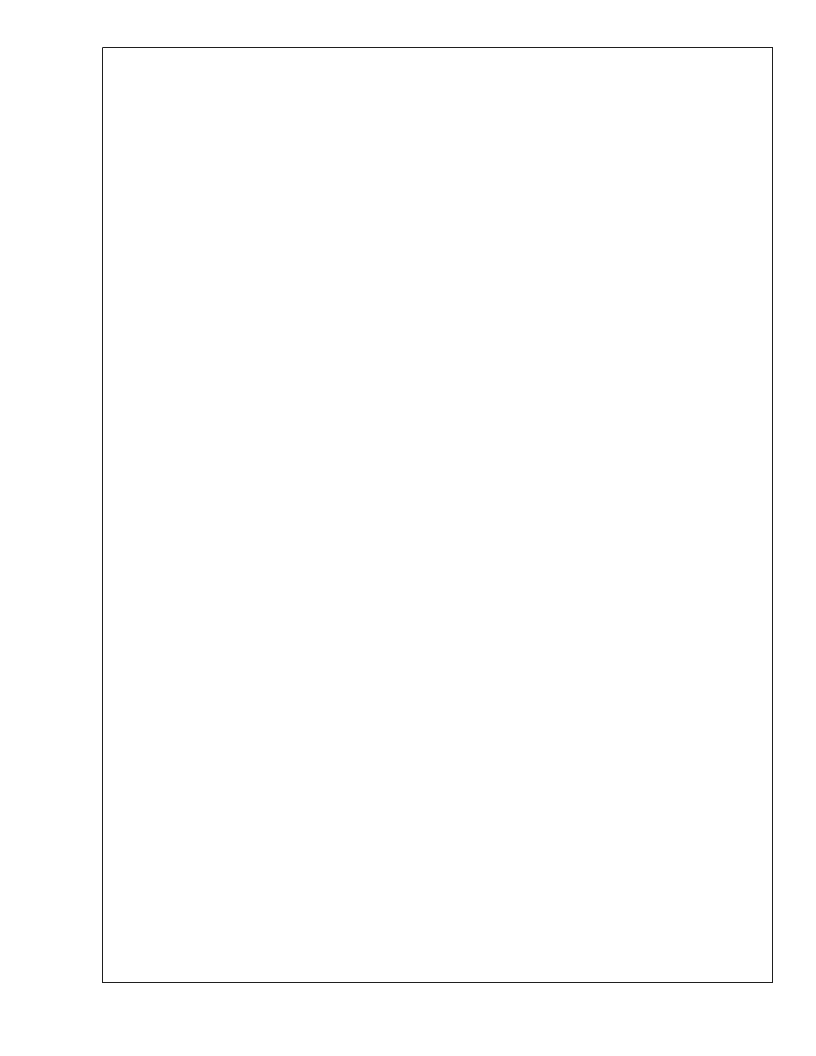
Application Information
(Continued)
power dissipation for the same conditions. The LM4913 has
two operational amplifiers driving a mono bridge load. The
maximum internal power dissipation operating in the bridge
mode is twice that of a single-ended amplifier. From Equa-
tion (3), assuming a 5V power supply and an 8W load, the
maximum BTL-mode power dissipation is 317mW.
P
DMAX-MONOBTL
= 2(V
DD
)
2
/ 2
π
2
R
L
:
The maximum power dissipation point given by Equation (3)
must not exceed the power dissipation given by Equation
(4):
P
DMAX’
= (T
JMAX
- T
A
) /
θ
JA
The LM4913’s TJMAX = 150C. In the MH package, the
LM4913’s
θ
is 46C/W. At any given ambient temperature
TA, use Equation (4) to find the maximum internal power
dissipation supported by the IC packaging. Rearranging
Equation (4) and substituting PDMAX for PDMAX ’ results in
Equation (5). This equation gives the maximum ambient
temperature that still allows maximum mono BTL power
dissipation without violating the LM4913’s maximum junction
temperature.
T
A
= T
JMAX
- P
DMAX-MONOBTL
θ
JA
For a typical application with a 5V power supply and an 8W
load, the maximum ambient temperature that allows maxi-
mum BTL power dissipation without exceeding the maximum
junction temperature is approximately 134C for the IBL
package.
T
JMAX
= P
DMAX-MONOBTL
θ
JA
+ T
A
Equation (6) gives the maximum junction temperature T
J-
MAX.
If the result violates the LM4913’s 150C T
JMAX
, reduce
the maximum junction temperature by decreasing the power
supply voltage or increasing the load resistance. Further
allowance should be made for increased ambient tempera-
tures.
The above examples assume that a device is a surface
mount part operating around the maximum power dissipation
point. Since internal power dissipation is a function of output
power, higher ambient temperatures are allowed as output
power or duty cycle decreases. If the result of Equation (3) is
greater than that of Equation (4), then decrease the supply
voltage, increase the load impedance, or reduce the ambient
temperature. If these measures are insufficient, a heat sink
can be added to reduce
θ
. The heat sink can be created
using additional copper area around the package, with con-
nections to the ground pin(s), supply pin and amplifier output
pins. External, solder attached SMT heatsinks such as the
Thermalloy 7106D can also improve power dissipation.
When adding a heat sink, the
θ
is the sum of
θ
,
θ
CS
, and
θ
. (
θ
is the junction-to-case thermal impedance,
θ
is
the case-to-sink thermal impedance, and qSA is the sink-to-
ambient thermal impedance.) Refer to the Typical Perfor-
mance Characteristics curves for power dissipation informa-
tion at lower output power levels.
Bridge Mode
(3)
(4)
(5)
(6)
EXPOSED-DAP PACKAGE PCB MOUNTING
CONSIDERATIONS
The LM4913’s exposed-DAP (die attach paddle) package
provides a low thermal resistance between the die and the
PCB to which the part is mounted and soldered. This low
thermal resistance is achieved by soldering the DAP to a
copper pad on the PCB. The copper pad’s dimensions
should match the DAP’s. The copper pad should then con-
nect to a larger copper area. This area can be on the
component side, in an inner layer in a multi-layer board, or
on the board’s back side. This connection from the DAP, to
the DAP pad, and finally to a larger copper area allows rapid
heat transfer away from the die to the surrounding air. The
result is a low voltage audio power amplifier that produces
2.0W at =1% THD+N with a 4
load. This high power is
achieved through careful consideration of necessary thermal
design. Failing to optimize thermal design may compromise
the LM4913’s high power performance and activate un-
wanted, though necessary, thermal shutdown protection.
The MH package must have its DAP soldered to a copper
pad on the PCB. The DAP’s PCB copper pad is connected to
a large plane of continuous unbroken copper. This plane
forms a thermal mass, and heat sink, and radiation area.
Place the heat sink area on either outside plane in the case
of a two-sided PCB, or on an inner layer of a board with more
than two layers. Connecting to a ground plane is permis-
sible. Connect the DAP copper pad to the inner layer or
backside copper heat sink area with 4(2x2) vias. The via
diameter should be 0.012in-0.013in with a 1.27mm pitch.
Ensure efficient thermal conductivity by plating-through and
solder-filling the vias.
Best thermal performance is achieved with the largest prac-
tical copper heatsink area. If the heatsink and amplifier share
the same PCB layer, a nominal 2.5in2 (min) area is neces-
sary for 5V operation with a 4
load. The heatsink area
should be 5in2 (min) when placed on a layer different from
that used by the LM4913. The last two area recommenda-
tions apply for 25C ambient temperature. Increase the area
to compensate for ambient temperatures above 25C. In all
circumstances and conditions, the junction temperature
must be held below 150C to prevent activating the
LM4913’s thermal shutdown protection. The LM4913’s
power de-rating curve in the Typical Performance Character-
istics shows the maximum power dissipation versus tem-
perature.An example PCB layout for the LM4913’s exposed-
DAP package is shown in the Demonstration Board Layout
section.
PCB LAYOUT AND SUPPLY REGULATION
CONSIDERATIONS FOR DRIVING 4
LOADS
Power dissipated by a load is a function of the voltage swing
across the load and the load’s impedance. As load imped-
ance decreases, load dissipation becomes increasingly de-
pendent on the interconnect (PCB trace and wire) resistance
between the amplifier output pins and the load’s connec-
tions. Residual trace resistance causes a voltage drop,
which results in power dissipated in the trace and not in the
load as desired. For example, 0.1W trace resistance re-
duces the output power dissipated by a 4
load from 1.9W
to 2W. This problem of decreased load dissipation is exac-
erbated as load impedance decreases. Therefore, to main-
tain the highest load dissipation and widest output voltage
swing, PCB traces that connect the output pins to a load
must be as wide as possible.
Poor power supply regulation adversely affects maximum
output power. A poorly regulated supply’s output voltage
decreases with increasing load current. Reduced supply
voltage causes decreased headroom, output signal clipping,
and reduced output power. Even with tightly regulated sup-
plies, trace resistance creates the same effects as poor
supply regulation. Therefore, make the power supply traces
as wide as possible to maintain full output voltage swing.
L
www.national.com
10