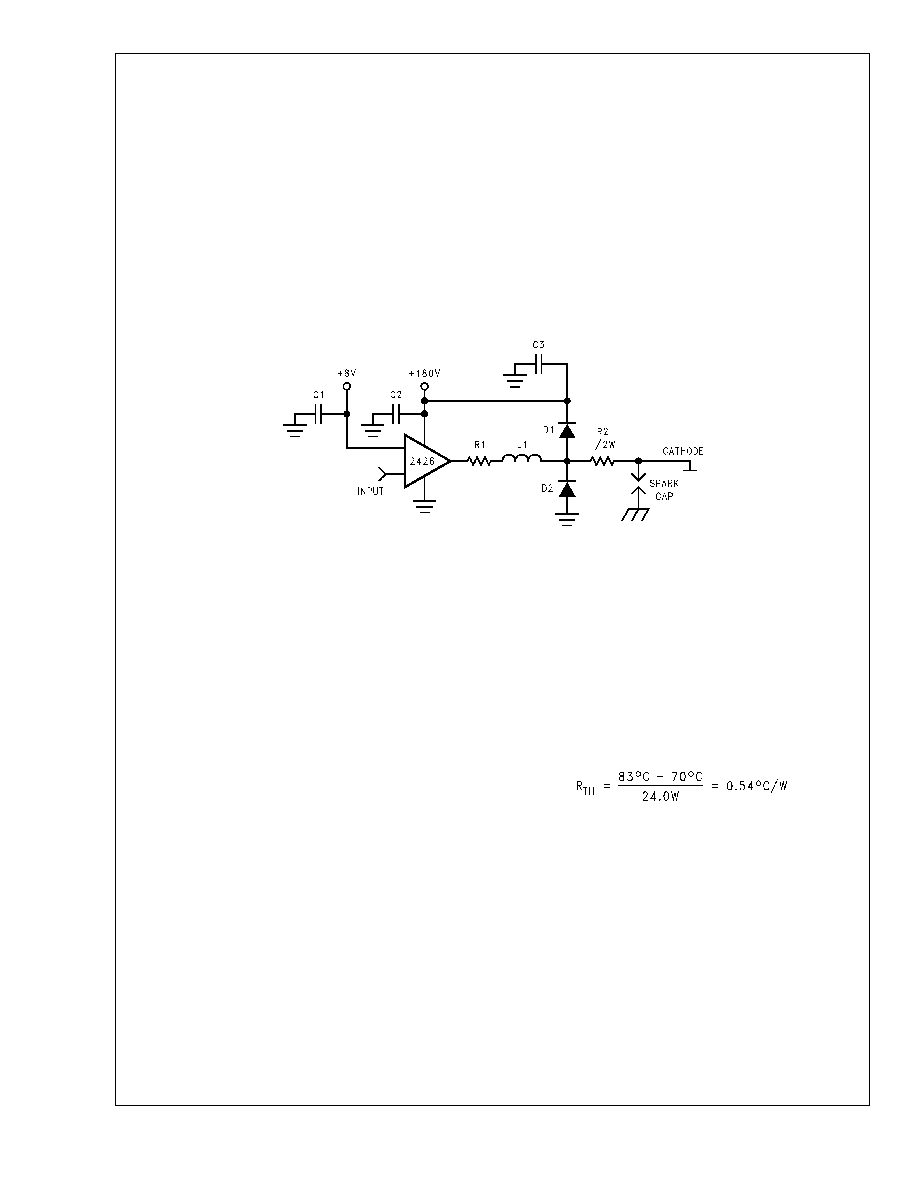
Application Hints (Continued)
voltage, but to a value that is much higher than allowable on
the LM2426. This fast, high voltage, high energy pulse can
damage the LM2426 output stage. The application circuit
shown in
Figure 13 is designed to help clamp the voltage at
the output of the LM2426 to a safe level. The clamp diodes,
D1 and D2, should have a fast transient response, high peak
current rating, low series impedance and low shunt capaci-
tance. 1SS83 or equivalent diodes are recommended. D1
and D2 should have short, low impedance connections to
V
CC and ground respectively. The cathode of D1 should be
located very close to a separately decoupled bypass capaci-
tor (C3 in
Figure 13). The ground connection of D2 and the
decoupling capacitor should be very close to the LM2426
ground. This will significantly reduce the high frequency
voltage transients that the LM2426 would be subjected to
during an arcover condition. Resistor R2 limits the arcover
current that is seen by the diodes while R1 limits the current
into the LM2426 as well as the voltage stress at the outputs
of the device. R2 should be a 12W solid carbon type resistor.
R1 can be a 14W metal or carbon film type resistor. Having
large value resistors for R1 and R2 would be desirable, but
this has the effect of increasing rise and fall times. Inductor
L1 is critical to reduce the initial high frequency voltage
levels that the LM2426 would be subjected to. The inductor
will not only help protect the device but it will also help
minimize rise and fall times as well as minimize EMI. For
proper arc protection, it is important to not omit any of the arc
EFFECT OF LOAD CAPACITANCE
Figure 7 shows the effect of increased load capacitance on
the speed of the device. This demonstrates the importance
of knowing the load capacitance in the application.
EFFECT OF OFFSET
Figure 8 shows the variation in rise and fall times when the
output offset of the device is varied from 95 to 105V
DC. The
rise time shows a variation of less than 5% relative to the
center data point (100V
DC). The fall time shows a variation of
5% relative to the center data point.
THERMAL CONSIDERATIONS
Figure 9 shows the performance of the LM2426 in the test
circuit shown in
Figure 3 as a function of case temperature.
The figure shows that the rise and fall times of the LM2426
increase by approximately 7% and 6%, respectively, as the
case temperature increases from 50C to 70C. This corre-
sponds to a speed degradation of 3.5% and 3% for every
10C rise in case temperature.
Figure 10 shows the maximum power dissipation of the
LM2426 vs. Frequency when all three channels of the device
are driving an 8pF load with a 110V
PP alternating one pixel
on, one pixel off signal. The graph assumes a 72% active
time (device operating at the specified frequency) which is
typical in a TV application. The other 28% of the time the
device is assumed to be sitting at the black level (165V in
this case). This graph gives the designer the information
needed to determine the heat sink requirement for his appli-
cation. The designer should note that if the load capacitance
is increased the AC component of the total power dissipation
will also increase.
the LM2426. For example, if the maximum bandwith needed
will be 30MHz, the power dissipated will be 24.0W (from
temperature is 83C when 24.0W is dissipated. If the maxi-
mum expected ambient temperature is 70C, then a maxi-
mum heatsink thermal resistance can be calculated:
This example assumes a capacitive load of 8pF and no
resistive load.
OPTIMIZING TRANSIENT RESPONSE
Referring to
Figure 13, there are three components (R1, R2
and L1) that can be adjusted to optimize the transient re-
sponse of the application circuit. Increasing the values of R1
and R2 will slow the circuit down while decreasing over-
shoot. Increasing the value of L1 will speed up the circuit as
well as increase overshoot. It is very important to use induc-
tors with very high self-resonant frequencies, preferably
above 300 MHz. Ferrite core inductors from J.W. Miller
Magnetics (part # 78FRTBDk) were used for optimizing the
performance of the device in the NSC application board. The
good starting point for the evaluation of the LM2426. Using a
variable resistor for R1 will simplify finding the value needed
20049010
FIGURE 13. One Channel of the LM2426 with the Recommended Application Circuit
LM2426
www.national.com
6