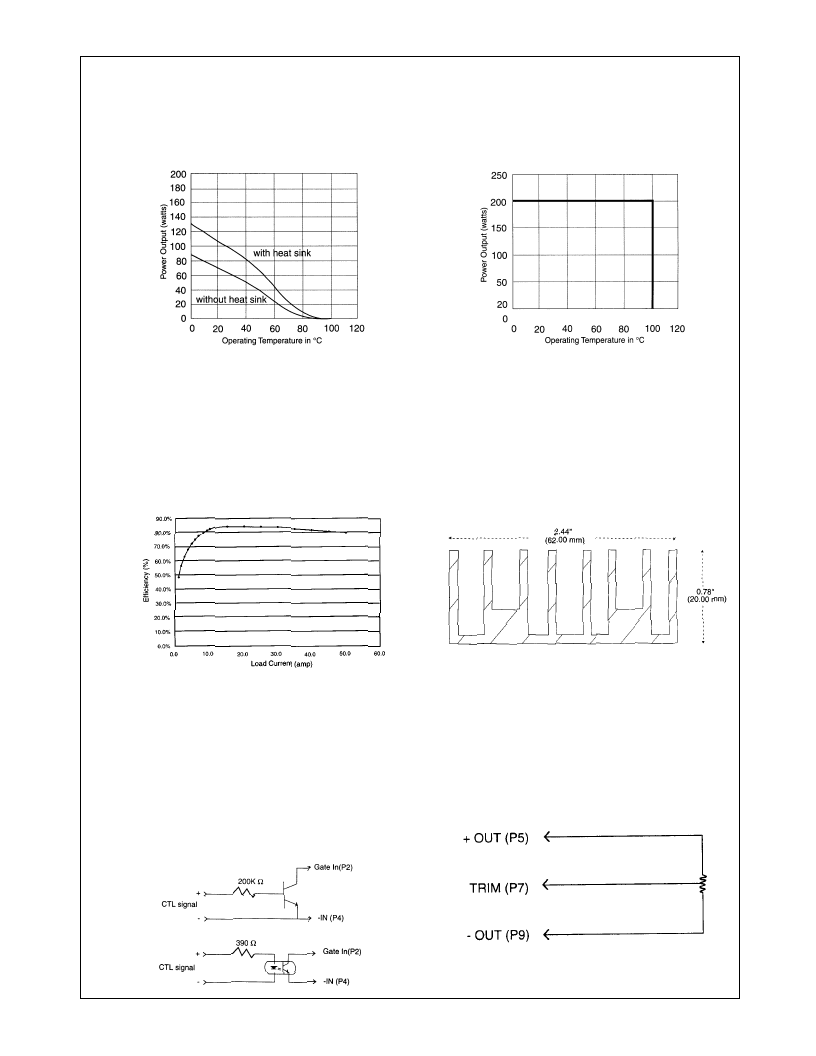
57
Application Notes
Thermal Consideration
Graph A shows the output power derating (in watts) with heat sink and without heat sink at various ambient tem-
peratures in still air conditions. If appropriate forced air is used with or without a heat sink, there is no power der-
ation as illustrated in Graph B. In such a case, the converter can be operated at its full output power rating.
Graph A:
Output Power Derating in Still Air
Conversion Efficiency
The graph below shows load current vs.
conversion efficiency specific to IBT200-301 only.
Graphs for other models available upon request.
Gate Control
A remote on-off control pin is provided to enable
or disable the converter. When the Gate-In Pin 2
is at logic high (2.8 to 7V) or open circuited, the
converter is enabled. At logic low (<2.8V) the con-
verter is then disabled. If the control signal
has a common return with the primary side, one
can use a NPN transistor circuit to enable/disable
the converter. If the control signal is from the sec-
ondary, or anywhere else, an opto-coupler circuit
can be used.
Graph B:
Output Power With Forced Air
Heat Sink
The converter can be operated at full-load with
appropriate forced air cooling or by using a
lower thermal resistance heat sink.
Material: Aluminum Extrusion Dimensions: 2.44 “ x 0.78” x 4.6”
Weight: 135 grams(0.3 lbs) Thermal Impedance: 3.0°C/W
Output Trimming
Approximately
±
10% output voltage trimming
can be achieved by adding a potentiometer.
The recommended circuit connection technique
is shown below. The suggested minimum
resistance value is 5.1K .
Load Current vs Efficiency