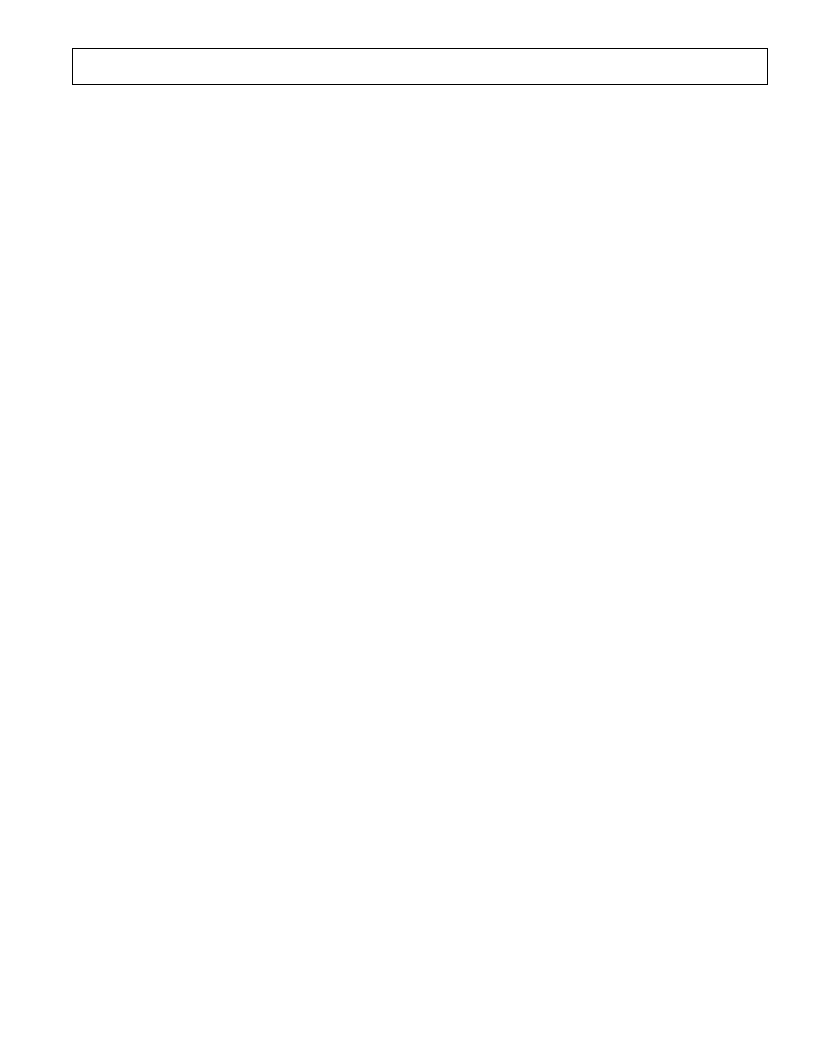
ADP3801/ADP3802
–7–
REV. 0
APPLICATIONS SECTION
PRODUCT DESCRIPTION
The ADP3801 and ADP3802 are complete Li-Ion battery charg-
ing ICs. Combined with a microcontroller, they also function as
voltage limited,
μ
C programmable constant current source chargers
for NiCad and NiMH chemistries. Utilizing an external PMOS
pass transistor, the devices realize a buck type constant current,
constant voltage (CCCV) charger controller that is capable of
charging two separate battery packs for such applications as
portable computer chargers and cellular phone chargers. The
Functional Block Diagram shows the ICs’ functional blocks,
which are detailed below:
A/B SELECT MUX—Two-channel multiplexer for charging
two battery stacks.
FINAL BATTERY VOLTAGE PROGRAM—Multiplexer to
program 4.2 V, 8.4 V, or 12.6 V final battery voltage.
VOLTAGE LOOP AMP—GM-type amplifier to control
the final battery voltage. It includes a built-in overvoltage
comparator.
EOC
COMPARATOR—End-of-charge detection output to
signal when the battery is fully charged.
BATTERY VOLTAGE ADJUST—Amplifier to adjust the
final battery voltage up to
±
10%.
CURRENT LOOP AMP—High-side-current-sense amplifier
to sense and control the charge current at a programmable
level. It includes an overcurrent comparator.
PWM—Pulsewidth modulator and oscillator (ADP3801-
200 kHz, ADP3802-500 kHz).
GATE DRIVE—Gate drive to control an external pass tran-
sistor. It includes a clamp to limit the drive voltage to protect
the external PMOS.
LDO + REFERENCE—3.3 V low dropout regulator to sup-
ply an external microcrontroller and for on-chip supply. In-
cludes an internal precision reference (VREF = VL/2).
SHUTDOWN—Logic input to shut down the charger. The
LDO remains on.
UVLO—Undervoltage lockout circuit to shut down the charger
for low supply voltages.
RESET—Active LOW output to reset external logic on power-
up.
During charging, the ADP3801/ADP3802 maintains a constant,
programmable charge current. The high side current sense
amplifier has low offset allowing the use of a low voltage drop
for current sensing: 165 mV for the maximum charge current.
The input common-mode range extends from ground to
VCC – 2 V ensuring current control over the full charging volt-
age of the battery, including a short circuit condition. A high
impedance dc voltage input (ISET) is provided for program-
ming the charge current over a wide range. When the battery
voltage approaches its final limit, the part automatically trans-
fers to voltage control mode. Both the current control loop and
the voltage control loop share the same compensation pin mini-
mizing the number of external components. An internal com-
parator monitors the charge current to detect the end-of-charge
(
EOC
). When the current decreases such that V
CS
≤
8 mV, the
EOC
output pulls low.
A 3.3 V LDO is used to generate a regulated supply for internal
circuitry. Additionally, the LDO can deliver up to 10 mA of
current to power external circuitry such as a microcontroller. An
Undervoltage Lockout (UVLO) circuit is included to safely shut
down the charging circuitry when the input voltage drops below
its minimum rating. A shutdown pin is also provided to turn off
the charger when, for example, the battery has been fully charged.
The LDO remains active during shutdown or UVLO and has a
quiescent current of 110
μ
A.
Battery Charging Overview
Figure 20 shows a simplified Buck type battery charger applica-
tion circuit for the ADP3801/ADP3802. When a discharged
battery is first placed in the charger, the battery voltage is well
below the final charge voltage, so the current sense amplifier
controls the charge loop in constant current mode. The charge
current creates a voltage drop across the sense resistor R
CS
. This
voltage drop is buffered and amplified by amplifier GM1. Am-
plifier GM2 compares the output of GM1 to an external current
control voltage provided at the ISET pin and servos the charger
loop to make these voltages equal. Thus, the charge current is
programmed using the ISET input voltage.
The output of GM2 is analog “OR’ed” with the output of GM3,
the voltage loop amplifier. Only one or the other amplifier con-
trols the charge loop at any given time. As the battery voltage
approaches its final voltage, GM3 comes into balance. As this
occurs, the charge current decreases, unbalancing GM2, and
control of the feedback loop naturally transfers to GM3.
The ADP3801/ADP3802 can control the charging of two inde-
pendent battery stacks or a single battery stack. The A/B SELECT
MUX has a logic input to choose between the two batteries. See
Figure 31 for more information on dual battery charging. The
output of the multiplexer is applied to a precision thin-film
resistor string to divide down the battery voltage. The final
battery voltage is chosen by selecting the proper resistor divider
tap with the PROG multiplexer. The output of this mux goes
directly to the input of GM3, comparing the divided down
battery voltage to the internal reference. To guarantee
±
0.75%
accuracy, a high precision internal reference and high accuracy
thin film resistors are used. Including these components on-
chip saves the significant cost and design effort of adding them
externally.