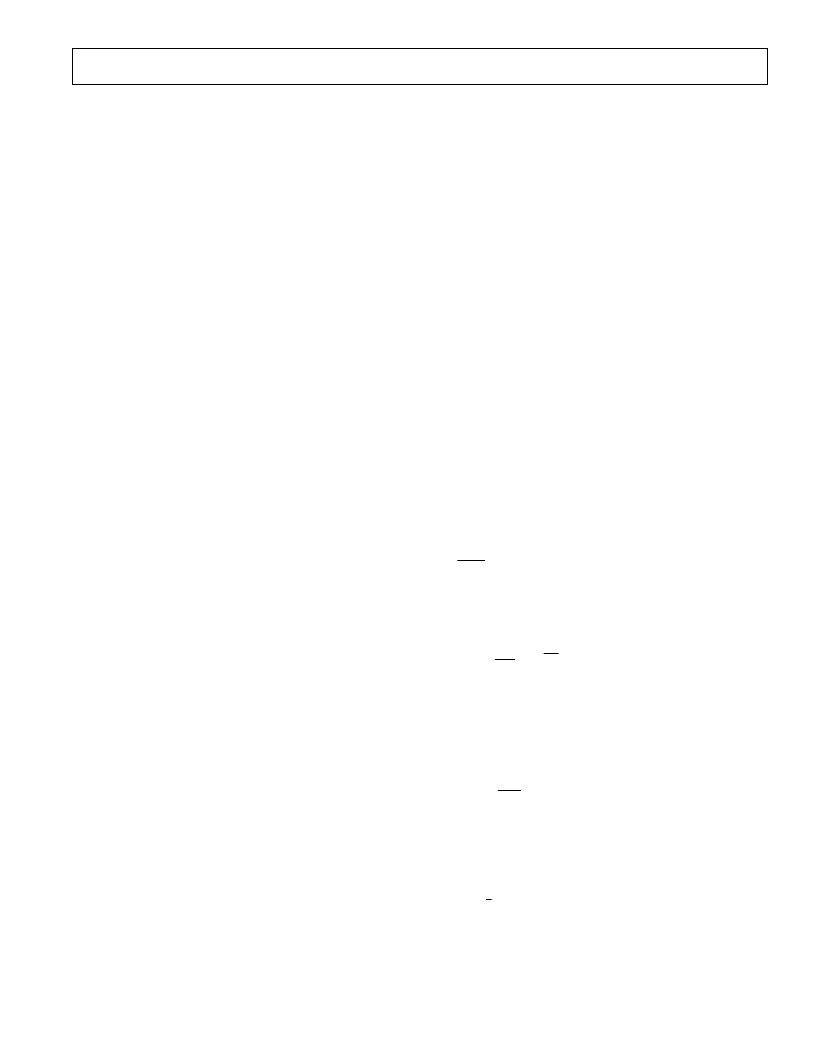
ADP1109
–5–
REV. 0
APPLICAT ION INFORMAT ION
T HE ORY OF OPE RAT ION
T he ADP1109 is a flexible, low power switch-mode power sup-
ply (SMPS) controller for step-up dc/dc converter applications.
T his device uses a gated-oscillator technique to provide very
high performance with low quiescent current. For example,
more than 2 W of output power can be generated from a +5 V
source, while quiescent current is only 450
μ
A.
A functional block diagram of the ADP1109 is shown on page 1.
T he internal 1.25 V reference is connected to one input of the
comparator, while the other input is externally connected (via
the FB pin) to a feedback network connected to the regulated
output. When the voltage at the FB pin falls below 1.25 V, the
120 kHz oscillator turns on. A driver amplifier provides base
drive to the internal power switch, and the switching action
raises the output voltage. When the voltage at the FB pin ex-
ceeds 1.25 V, the oscillator is shut off. While the oscillator is off,
the ADP1109 quiescent current is only 450
μ
A. T he comparator
includes a small amount of hysteresis, which ensures loop stabil-
ity without requiring external components for frequency com-
pensation.
A shutdown feature permits the oscillator to be shut off. Hold-
ing
SHUTDOWN
low will disable the oscillator, and the
ADP1109’s quiescent current will remain 450
μ
A.
T he output voltage of the ADP1109 is set with two external
resistors. T hree fixed-voltage models are also available: the
ADP1109-3.3 (+3.3 V), ADP1109-5 (+5 V) and ADP1109-12
(+12 V). T he fixed-voltage models are identical to the ADP1109,
except that laser-trimmed voltage-setting resistors are included on
the chip. On the fixed-voltage models of the ADP1109, simply
connect the SENSE pin (Pin 8) directly to the output voltage.
COMPONE NT SE LE CT ION
General Notes on Inductor Selection
When the ADP1109 internal power switch turns on, current
begins to flow in the inductor. Energy is stored in the inductor
core while the switch is on, and this stored energy is then trans-
ferred to the load when the switch turns off.
T o specify an inductor for the ADP1109, the proper values of
inductance, saturation current and dc resistance must be deter-
mined. T his process is not difficult, and specific equations are
provided in this data sheet. In general terms, however, the induc-
tance value must be low enough to store the required amount of
energy (when both input voltage and switch ON time are at a
minimum), but high enough that the inductor will not saturate
when both V
IN
and switch ON time are at their maximum val-
ues. T he inductor must also store enough energy to supply the
load, without saturating. Finally, the dc resistance of the induc-
tor should be low, so that excessive power will not be wasted by
heating the windings. For most ADP1109 applications, an in-
ductor of 10
μ
H to 47
μ
H, with a saturation current rating of
300 mA to 1 A and dc resistance <0.4
is suitable. Ferrite core
inductors that meet these specifications are available in small,
surface-mount packages. Air-core inductors, as well as RF chokes,
are unsuitable because of their low peak current ratings.
T he ADP1109 is designed for applications where the input
voltage is fairly stable, such as generating +12 V from a +5 V
logic supply. T he ADP1109 does not have an internal switch
current limiting circuit, so the inductor may saturate if the input
voltage is too high. T he ADP1111 or ADP3000 should be
considered for battery powered and similar applications where
the input voltage varies.
T o minimize Electro-Magnetic Interference (EMI), a toroid or
pot core type inductor is recommended. Rod core inductors are
a lower cost alternative if EMI is not a problem.
Calculating the Inductor Value
Selecting the proper inductor value is a simple, two-step process:
1. Define the operating parameters: minimum input voltage,
maximum input voltage, output voltage and output current.
2. Calculate the inductor value, using the equations in the fol-
lowing section.
Inductor Selection
In a step-up, or boost, converter (Figure 1), the inductor must
store enough power to make up the difference between the input
voltage and the output voltage. T he inductor power is calculated
from the equation:
(
where
V
D
is the diode forward voltage (
<
0.5 V for a 1N5818
Schottky). Energy is stored in the inductor only while the
ADP1109 switch is ON, so the energy stored in the inductor on
each switching cycle must be must be equal to or greater than:
P
L
=
V
OUT
+
V
D
V
IN MIN
)
)
×
I
OUT
(
)
(1)
P
L
f
OSC
(2)
in order for the ADP1109 to regulate the output voltage. When the
internal power switch turns ON, current flow in the inductor
increases at the rate of:
I
L
t
( )
=
V
IN
R
1
e
R
t
L
(3)
where
L
is in Henrys and R' is the sum of the switch equivalent
resistance (typically 0.8
at +25
°
C) and the dc resistance of
the inductor. In most applications, the voltage drop across the
switch is small compared to V
IN
so a simpler equation can be
used:
I
L
t
( )
=
V
IN
L
t
(4)
Replacing
t
in the above equation with the ON time of the
ADP1109 (5.5
μ
s, typical) will define the peak current for a
given inductor value and input voltage. At this point, the induc-
tor energy can be calculated as follows:
E
L
=
1
2
L
×
I
2
peak
(5)