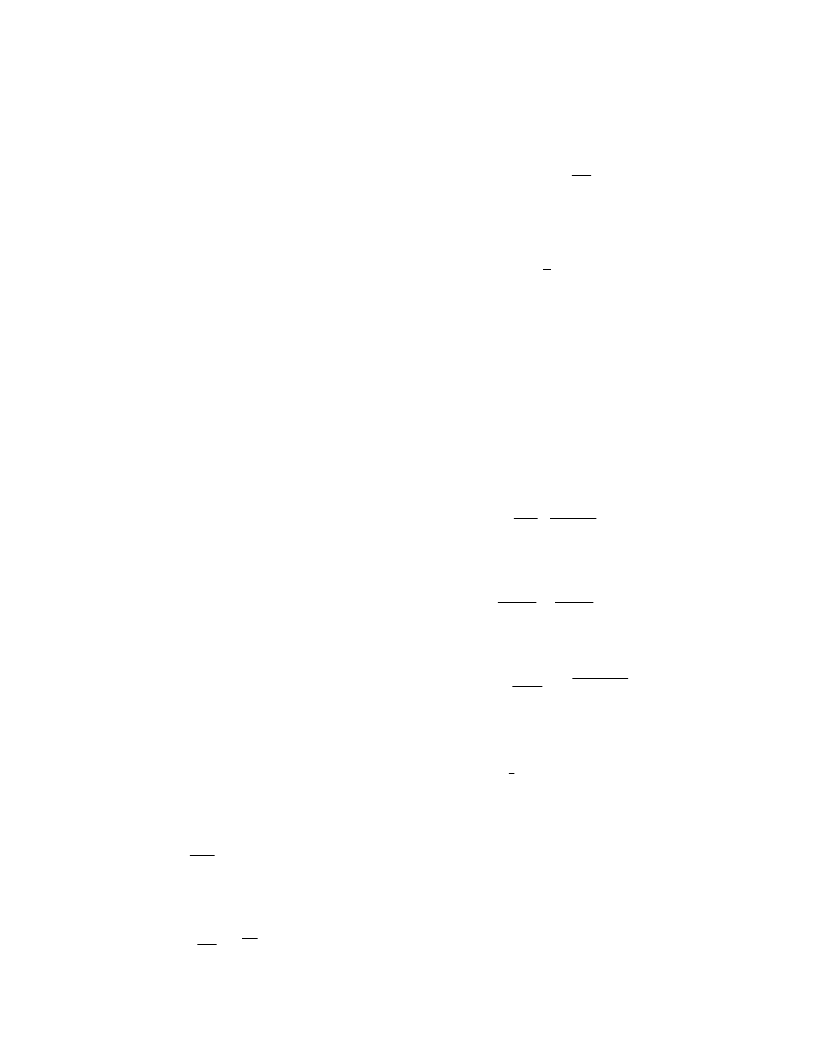
ADP1073
–6–
REV. 0
COMPONENT SELECTION
General Notes on Inductor Selection
When the ADP1073 internal power switch turns on, current
begins to flow in the inductor. Energy is stored in the inductor
core while the switch is on, and this stored energy is then trans-
ferred to the load when the switch turns off. Both the collector
and the emitter of the switch transistor are accessible on the
ADP1073, so the output voltage can be higher, lower or of
opposite polarity than the input voltage.
To specify an inductor for the ADP1073, the proper values of
inductance, saturation current and dc resistance must be deter-
mined. This process is not difficult, and specific equations for
each circuit configuration are provided in this data sheet.
In general terms, however, the inductance value must be low
enough to store the required amount of energy (when both
input voltage and switch ON time are at a minimum) but high
enough that the inductor will not saturate when both V
IN
and
switch ON time are at their maximum values. The inductor
must also store enough energy to supply the load without satu-
rating. Finally, the dc resistance of the inductor should be low
so that excessive power will not be wasted by heating the
windings. For most ADP1073 applications, an 82
μ
H to
1000
μ
H inductor with a saturation current rating of 300 mA to
1 A is suitable. Ferrite core inductors that meet these specifica-
tions are available in small, surface-mount packages.
To minimize Electro-Magnetic Interference (EMI), a toroid or
pot core type inductor is recommended. Rod core inductors are
a lower cost alternative if EMI is not a problem.
Calculating the Inductor Value
Selecting the proper inductor value is a simple three-step process:
1. Define the operating parameters: minimum input voltage,
maximum input voltage, output voltage and output current.
2. Select the appropriate conversion topology (step-up, step-
down or inverting).
3. Calculate the inductor value, using the equations in the
following sections.
Inductor Selection—Step-Up Converter
In a step-up, or boost, converter (Figure 15), the inductor must
store enough power to make up the difference between the
input voltage and the output voltage. The power that must be
stored is calculated from the equation:
P
L
=
V
OUT
+
V
D
–
V
IN
(
MIN
)
where
V
D
is the diode forward voltage (
≈
0.5 V for a 1N5818
Schottky). Energy is only stored in the inductor while the
ADP1073 switch is ON, so the energy stored in the inductor on
each switching cycle must be must be equal to or greater than:
P
L
f
OSC
in order for the ADP1073 to regulate the output voltage.
When the internal power switch turns ON, current flow in the
inductor increases at the rate of:
(
)
×
I
OUT
(
)
(1)
(2)
I
L
(
t
)
=
V
IN
R
′
1–
e
–
R
′
t
L
(3)
where L is in henrys and R' is the sum of the switch equivalent
resistance (typically 0.8
at +25
°
C) and the dc resistance of
the inductor. If the voltage drop across the switch is small com-
pared to V
IN
, a simpler equation can be used:
I
L
(
t
)
=
V
IN
Replacing
t
in the above equation with the ON time of the ADP1073
(38
μ
s, typical) will define the peak current for a given inductor
value and input voltage. At this point, the inductor energy can
be calculated as follows:
E
L
=
1
2
L
×
I
2
PEAK
As previously mentioned, E
L
must be greater than P
L
/f
OSC
so the
ADP1073 can deliver the necessary power to the load. For best
efficiency, peak current should be limited to 1 A or less. Higher
switch currents will reduce efficiency because of increased satu-
ration voltage in the switch. High peak current also increases
output ripple. As a general rule, keep peak current as low as
possible to minimize losses in the switch, inductor and diode.
In practice, the inductor value is easily selected using the equa-
tions above. For example, consider a supply that will generate
5 V at 25 mA from two alkaline batteries with a 2 V end-of-life
voltage. The inductor power required is, from Equation 1:
L
t
(4)
(5)
P
L
=
(5
V
+
0.5
V
–2
V
)
×
(25
mA
)
=
87.5
mW
On each switching cycle, the inductor must supply:
P
L
f
OSC
=
87.5
mW
19
kHz
=
4.6
μ
J
Since the inductor power is low, the peak current can also be
low. Assuming a peak current of 100 mA as a starting point,
Equation 4 can be rearranged to recommend an inductor value:
V
IN
I
L
(
MAX
)
Substituting a standard inductor value of 470
μ
H, with 1.2
dc
resistance, will produce a peak switch current of:
L
=
t
=
2
V
100
mA
38
μ
s
=
760
μ
H
I
PEAK
=
2
V
2.0
1–
e
–2.0
×
38
μ
s
470
μ
H
=
149
mA
Once the peak current is known, the inductor energy can be
calculated from Equation 5:
E
L
=
1
μ
H
)
×
(149
mA
)
2
=
5.2
μ
J
The inductor energy of 5.2
μ
J is greater than the P
L
/f
OSC
re-
quirement of 4.6
μ
J, so the 470
μ
H inductor will work in this
application. The optimum inductor value can be determined
by substituting other inductor values into the same equations.
When selecting an inductor, the peak current must not exceed
the maximum switch current of 1.5 A.
The peak current must be evaluated for both minimum and
maximum values of input voltage. If the switch current is high
when V
IN
is at its minimum, then the 1.5 A limit may be exceeded
at the maximum value of V
IN
. In this case, the ADP1073’s current