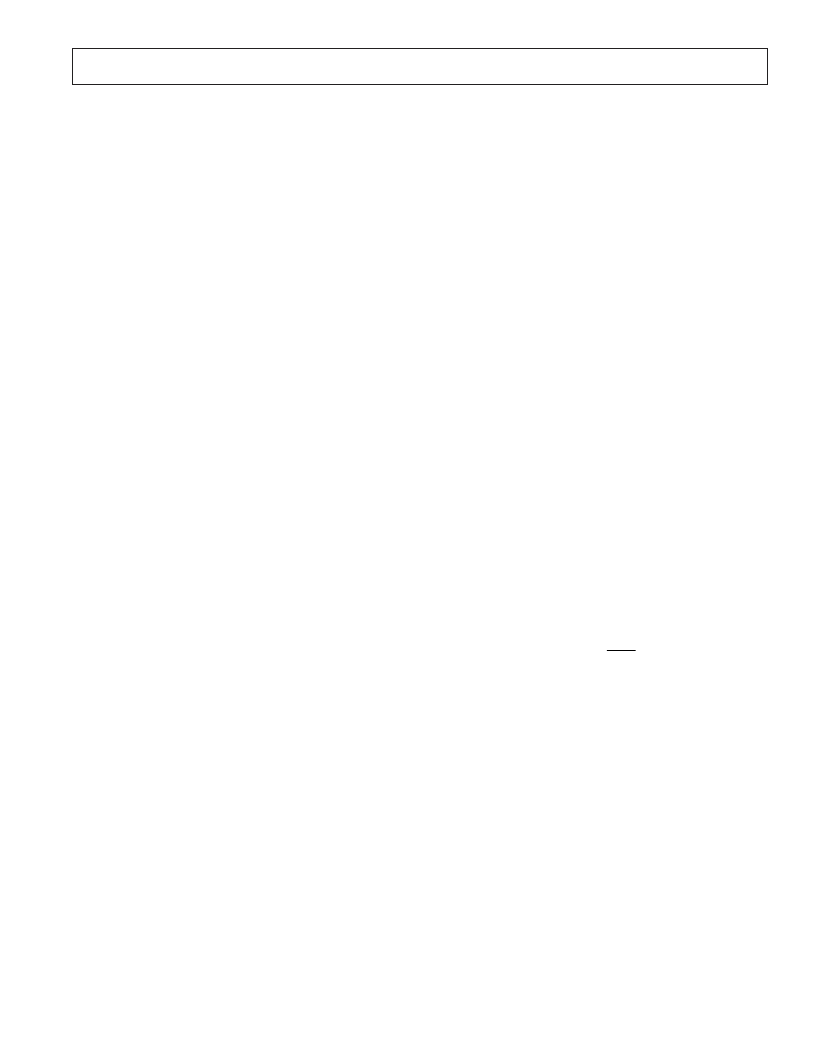
ADDC02803SC/ADDC02805SA
REV. A
–15–
Circuit Setup for EMI Test
Figure 23 shows a schematic of the test setup used for the EMI
measurements discussed above. The output of the converter is
connected to a resistive load designed to draw full power. There
is a 0.1
μ
F capacitor placed across this resistor that typifies by-
pass capacitance normally used in this application. At the input
of the converter there are two differential capacitors (the larger
one having a series resistance) and two small common-mode
capacitors connected to case ground. The case itself was con-
nected to the metal ground plane in the test chamber. For the
RE102 test, a metal screen box was used to cover both the con-
verter and its load (but not the two meters of input power lead
cables). This box was also electrically connected to the metal
ground plane.
With regard to the components added to the input power lines,
the 100
μ
F capacitor with its 1
series resistance is required to
achieve system stability when the unit is powered through the
LISNs, as the MIL-STD-461D standard requires. These
LISNs have a series inductance of 50
μ
H at low frequencies,
giving a total differential inductance of 100
μ
H. As explained
earlier in the System Instability section, such a large series
source inductance will cause an instability as it interacts with the
converter’s negative incremental input resistance unless some
corrective action is taken. The 100
μ
F capacitor and 1
resis-
tor provide the stabilization required.
It should be noted that the values of these stabilization components
are appropriate for a single converter load. If the system makes
use of several converters, the values of the components will need
to be slightly changed, but not such that they are repeated for
every converter. It should also be noted that most system appli-
cations will not have a source inductance as large as the 100
μ
H
built into the LISNs. For those systems, a much smaller input
capacitor could be used.
Increasing Margin Between Specification Limit and
Measured Results
With regard to the 2
μ
F differential-mode capacitor and the two
82 nF common-mode capacitors, these components were in-
cluded in the test setup to augment the performance of the
power supply’s internal EMI filter. The values were chosen to
achieve the results shown in Figures 20 and 22. To increase the
margin between the specification limits and the measured emis-
sions, larger external component values could be used.
To do this it is useful to know that most of the emissions below
10 MHz, whether conducted or radiated, are due to differential-
mode currents flowing in the input power leads. To make the
emissions in this frequency range smaller, the differential ca-
pacitor value should be increased above 2
μ
F. Conversely, most
of the emissions above 10 MHz are due to common-mode cur-
rents; to make them smaller the common-mode capacitors
should be increased above the 82 nF value. In both cases it is
important to minimize the parasitic inductance of the capaci-
tors; the use of several smaller capacitors connected in parallel is
one way to achieve this.
Using larger valued capacitors than those shown in Figure 23 is
a good solution if an additional 6 dB–10 dB of margin is de-
sired. If, however, in an extremely sensitive application it is
desired to increase the margin by 20 dB or more, it may be
better to add both differential- and common-mode inductors to
the external components to make a higher order filter.
RELIABILITY CONSIDERATIONS
MTBF (Mean Time Between Failure) is a commonly used
reliability concept that applies to repairable items in which
failed elements are replaced upon failure. The expression for
MTBF is
MTBF = T/r
where:
T
= total operating time
r
= number of failures
In lieu of actual field data, MTBF can be predicted per
MIL-HDBK-217.
MTBF, Failure Rate and Probability of Failure:
A proper
understanding of MTBF begins with its relationship to lambda
(
λ
), which is the failure rate. If a constant failure rate is assumed,
then MTBF = 1/
λ
, or
λ
= 1/MTBF. If a power supply has an
MTBF of 1,000,000 hours, this does not mean it will last
1,000,000 hours before it fails. Instead, the MTBF describes
the failure rate. For 1,000,000 hours MTBF, the failure rate
during any hour is 1/1,000,000, or 0.0001%. Thus, a power
supply with an MTBF of 500,000 hours would have twice the
failure rate (0.0002%) of one with 1,000,000 hours.
What users should be interested in is the probability of a power
supply not failing prior to some time t. Given the assumption of
a constant failure rate, this probability is defined as
R
(
t
)
=
e
–
λ
t
where
R(t)
is the probability of a device not failing prior to some
time
t
.
If we substitute
λ
= 1/MTBF in the above formula, then the
expression becomes
R
(
t
)
=
e
–
t
MTBF
This formula is the correct way to interpret the meaning of
MTBF.
If we assume
t
= MTBF = 1,000,000 hours, then the probability
that a power supply will not fail prior to 1,000,000 hours of use
is e
–1
, or 36.8%. This is quite different from saying the power
supply will last 1,000,000 hours before it fails. The probability
that the power supply will not fail prior to 50,000 hours of use is
e
–0.05
, or 95%. For
t
= 10,000 hours, the probability of no fail-
ure is e
–0.01
, or 99%.
Temperature and Environmental Factors:
Although the
calculation of MTBF per MIL-HDBK-217 is a detailed process,
there are two key variables that give the manufacturer signi-
ficant leeway in predicting an MTBF rating. These two vari-
ables are temperature and environmental factor. For users to
properly compare MTBF numbers from two different manu-
facturers, the environmental factor and the temperature must
be identical. Contact the factory for MTBF calculations for
specific environmental factors and temperatures.