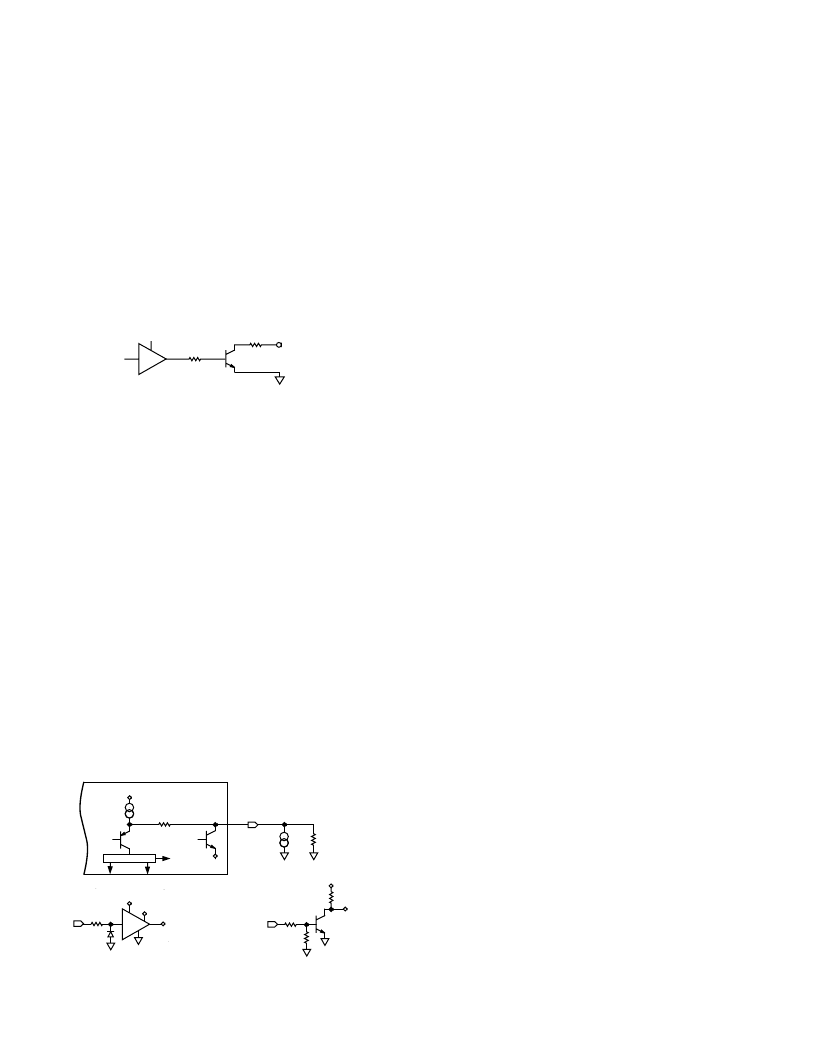
REV. A
AD8016
–12–
BIAS pin (I
BIAS
) and the supply current (I
Q
). A typical shut-
down I
Q
is less than 1 mA total. Alternatively, an external pull-
down resistor to ground or a current sink attached to the BIAS
pin can be used to set I
Q
to lower levels (see Figure 39). The
BIAS pin may be used in combination with the PWDN1 and
PWDN0 pins; however, diminished MTPR performance may
result when I
Q
is lowered too much. Current pulled away from
the BIAS pin will shunt away a portion of the internal bias cur-
rent. Setting PWDN1 or PWDN0 to Logic 0 also shunts away a
portion of the internal bias current. The reduction of quiescent
bias levels due to the use of PWDN1 and PWDN0 is consistent
with the percentages established in Table II. When PWDN0 alone
is set to Logic 0, and no other means of reducing the internal
bias currents is used, full-rate ADSL signals may be driven while
maintaining reasonable levels of MTPR.
R2
50k
BIAS
R1
*
3.3V LOGIC
2N3904
*R1 = 47k FOR 12V
S
OR +12V
S
,
R1 = 22k FOR 6V
S
.
Figure 38. Logic Drive of BIAS Pin for Complete Amplifier
Shutdown
THERMAL SHUTDOWN
The AD8016ARB and ARP have been designed to incorporate
shutdown protection against accidental thermal overload. In the
event of thermal overload, the AD8016 was designed to shut
down at a junction temperature of 165
°
C and return to normal
operation at a junction temperature 140
°
C The AD8016 will
continue to operate, cycling on and off, as long as the thermal
overload condition remains. The frequency of the protection
cycle depends on the ambient environment, severity of the ther-
mal overload condition, the power being dissipated and the ther-
mal mass of the PCB beneath the AD8016. When the AD8016
begins to cycle due to thermal stress, the internal shutdown
circuitry draws current out of the node connected in common
with the BIAS pin, while the voltage at the BIAS pin goes to the
negative rail. When the junction temperature returns to 140
°
C,
current is no longer drawn from this node and the BIAS pin
voltage returns to the positive rail. Under these circumstances,
the BIAS pin can be used to trip an alarm indicating the pres-
ence of a thermal overload condition.
Figure 39 also shows three circuits for converting this signal to a
standard logic level.
V
CC
+5V
BIAS
10k
ALARM
1/4 HCF 40109B
SGS - THOMSON
10k
+5V
100k
1M
BIAS
ALARM
MIN 350
OR
V
EE
10k
200 A
V
CC
BIAS
PWDN1
BIAS
OR
0
–
200 A
V = V
CC
–
0.2V
SHUT-
DOWN
AD8016
PWDN0
Figure 39. Shutdown and Alarm Circuit
APPLICATIONS
The AD8016ARP and AD8016ARB dual xDSL line driver
amplifiers are the most efficient xDSL line drivers available to
the market today. The AD8016 may be applied in driving modu-
lated signals including Discrete Multitone (DMT) in either
direction; upstream from Customer Premise Equipment (CPE)
to the Central Office (CO) and downstream from CO to CPE.
The most significant thermal management challenge lies in
driving downstream information from CO sites to the CPE.
Driving xDSL information downstream suggests the need to
locate many xDSL modems in a single CO site. The implication
is that several modems will be placed onto a single printed cir-
cuit board residing in a card cage located in a variety of ambient
conditions. Environmental conditioners such as fans or air con-
ditioning may or may not be available, depending on the density
of modems and the facilities contained at the CO site. To achieve
long-term reliability and consistent modem performance, designers
of CO solutions must consider the wide array of ambient condi-
tions that exist within various CO sites.
MULTITONE POWER RATIO OR MTPR
ADSL systems rely on Discrete Multitone (or DMT) modulation
to carry digital data over phone lines. DMT modulation appears
in the frequency domain as power contained in several individual
frequency subbands, sometimes referred to as tones or bins, each
of which is uniformly separated in frequency. (See Figure 1 for
example of downstream DMT signals used in evaluating MTPR
performance.) A uniquely encoded, Quadrature Amplitude Modu-
lation (QAM) signal occurs at the center frequency of each
subband or tone. Difficulties will exist when decoding these
subbands if a QAM signal from one subband is corrupted by the
QAM signal(s) from other subbands, regardless of whether the
corruption comes from an adjacent subband or harmonics of
other subbands. Conventional methods of expressing the output
signal integrity of line drivers, such as spurious free dynamic range
(SFDR), single-tone harmonic distortion or THD, two-tone
Intermodulation Distortion (IMD) and 3rd order intercept (IP3)
become significantly less meaningful when amplifiers are required
to drive DMT and other heavily modulated waveforms. A typical
xDSL downstream DMT signal may contain as many as 256
carriers (subbands or tones) of QAM signals. Multitone Power
Ratio (MTPR) is the relative difference between the measured
power in a typical subband (at one tone or carrier) versus the
power at another subband specifically selected to contain no QAM
data. In other words, a selected subband (or tone) remains open
or void of intentional power (without a QAM signal) yielding an
empty frequency bin. MTPR, sometimes referred to as the
“
empty
bin test,
”
is typically expressed in dBc, similar to expressing the
relative difference between single-tone fundamentals and 2nd or
3rd harmonic distortion components.
See Figure 1 for a sample of the ADSL downstream spectrum
showing MTPR results while driving 20.4 dBm of power onto a
100
line. Measurements of MTPR are typically made at the
output (line side) of ADSL hybrid circuits. (See Figure 46a for
an example of Analog Devices
’
hybrid schematic.) MTPR can
be affected by the components contained in the hybrid circuit,
including the quality of the capacitor dielectrics, voltage ratings
and the turns ratio of the selected transformers. Other compo-
nents aside, an ADSL driver hybrid containing the AD8016 can be
optimized for the best MTPR performance by selecting the turns
ratio of the transformers. The voltage and current demands from
the differential driver changes, depending on the transformer