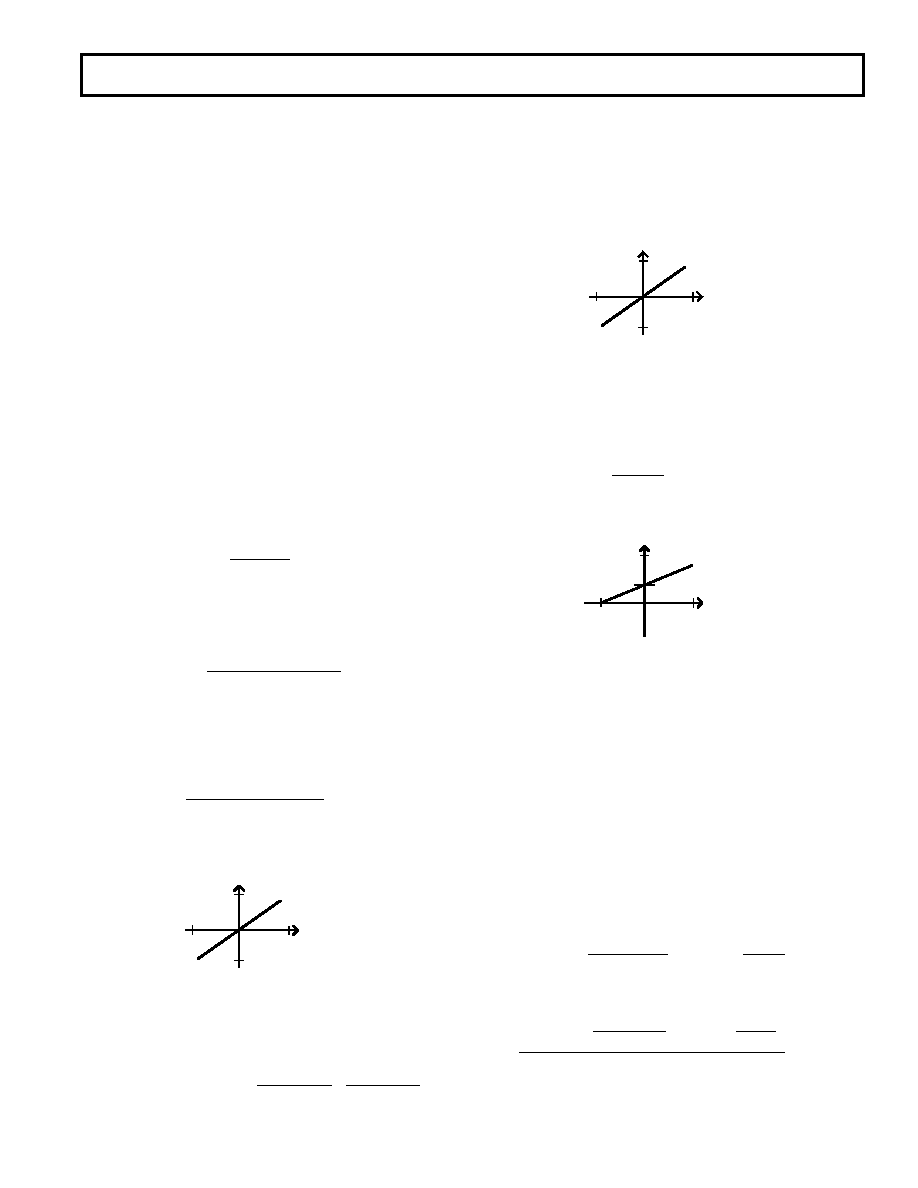
AD598
REV. A
–7–
8. C2, C3 and C4 are a function of the desired bandwidth of
the AD598 position measurement subsystem. They should
be nominally equal values.
C2 = C3 = C4 = 10
–4 Farad Hz/f
SUBSYSTEM (Hz)
If the desired system bandwidth is 250 Hz, then
C2 = C3 = C4 = 10
–4 Farad Hz/250 Hz = 0.4
F
See Figures 13, 14 and 15 for more information about
AD598 bandwidth and phase characterization.
9. In order to Compute R2, which sets the AD598 gain or full-
scale output range, several pieces of information are needed:
a. LVDT sensitivity, S
b. Full-scale core displacement, d
c. Ratio of manufacturer recommended primary drive level,
VPRI to (VA + VB) computed in Step 4.
LVDT sensitivity is listed in the LVDT manufacturer’s cata-
log and has units of millivolts output per volts input per inch
displacement. The E100 has a sensitivity of 2.4 mV/V/mil.
In the event that LVDT sensitivity is not given by the manu-
facturer, it can be computed. See section on Determining
LVDT Sensitivity.
For a full-scale displacement of d inches, voltage out of the
AD598 is computed as
VOUT = S ×
VPRI
(VA +VB)
× 500 A × R2 × d.
VOUT is measured with respect to the signal reference,
Pin 17 shown in Figure 7.
Solving for R2,
R2
=
VOUT × (VA +VB )
S
×V
PRI × 500 A × d
(1)
Note that VPRI is the same signal level used in Step 4 to
determine (VA + VB).
For VOUT = 20 V full-scale range (
±10 V) and d = 0.2 inch
full-scale displacement (
±0.1 inch),
R2
=
20V
× 2.70V
2.4
× 3 × 500 A × 0.2 =
75. 3 k
VOUT as a function of displacement for the above example is
shown in Figure 9.
+10
+0.1 d
0.1
–
10
–
V
OUT (VOLTS)
(INCHES)
Figure 9. VOUT (±10 V Full Scale)
vs. Core Displacement (
±0.1 Inch)
10. Selections of R3 and R4 permit a positive or negative output
voltage offset adjustment.
VOS = 1.2V × R2 ×
1
R 3
+ 5 k*
–
1
R4
+ 5 k*
(2)
*These values have a
±20% tolerance.
For no offset adjustment R3 and R4 should be open circuit.
To design a circuit producing a 0 V to +10 V output for a
displacement of
±0.1 inch, set V
OUT to +10 V, d = 0.2 inch
and solve Equation (1) for R2.
R2 = 37.6 k
This will produce a response shown in Figure 10.
+5
+0.1 d
0.1
–
5
–
(INCHES)
V
OUT (VOLTS)
Figure 10. VOUT (±5 V Full Scale)
vs. Core Displacement (
±0.1 Inch)
In Equation (2) set VOS = 5 V and solve for R3 and R4.
Since a positive offset is desired, let R4 be open circuit.
Rearranging Equation (2) and solving for R3
R 3
=
1.2
× R2
VOS
–5 k
= 4.02 k
Figure 11 shows the desired response.
+10
0.1
–
+0.1 d
+5
(INCHES)
V
OUT (VOLTS)
Figure 11. VOUT (0 V–10 V Full Scale)
vs. Displacement (
±0.1 Inch)
DESIGN PROCEDURE
SINGLE SUPPLY OPERATION
Figure 12 shows the single supply connection method.
For single supply operation, repeat Steps 1 through 10 of the
design procedure for dual supply operation, then complete the
additional Steps 11 through 14 below. R5, R6 and C5 are addi-
tional component values to be determined. VOUT is measured
with respect to SIGNAL REFERENCE.
11. Compute a maximum value of R5 and R6 based upon the
relationship
R5 + R6
≤ V
PS/100 A
12. The voltage drop across R5 must be greater than
2
+ 10 k*
1.2V
R4
+ 5 k
+ 250 A +
VOUT
4
× R2
Volts
Therefore
R5
≥
2
+10 k*
1.2 V
R4
+5k
+250 A +
VOUT
4
× R2
100
A
Ohms
*These values have
±20% tolerance.
Based upon the constraints of R5 + R6 (Step 11) and R5
(Step 12), select an interim value of R6.